The promise of high efficiency and small size brought by super-fast switching power supplies could be delayed by a lack of magnetic materials that are up to the task.
Leland Teschler | Executive Editor
Eyeball the schedule for APEC, considered the premier technical conference for power electronics, and you’ll notice a number of sessions devoted to magnetics. The interest in magnetic components stems from gallium-nitride and silicon-carbide semiconductors. These wide-bandgap semiconductors have on resistances and related losses that are one-tenth that of devices based on silicon which reduces both their inherent capacitance and resistor-capacitor time constant. The result is lower losses per switching cycle, a consequence that lets GaN and SiC-based switch-mode power supplies switch at much higher frequencies – sometimes on the order of hundreds of megahertz.
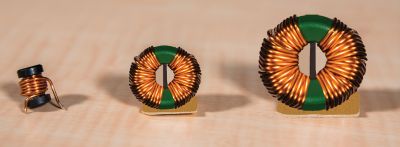
Therein lies the reason for the APEC sessions on magnetics. Operation at these higher frequencies can drastically reduce the size of the magnetic components involved in energy storage, but it is tough to find magnetic materials that can operate at such frequencies without experiencing a lot of energy loss. So the quest is on to find better ones.
To understand the problem, and to comprehend some of the finer points made at APEC presentations, it pays to be familiar with the fundamental parameters that describe magnetic materials and their energy storage capacity. Several materials now under investigation show promise for improving some of these parameters but generally at the expense of others.
Hard vs. soft magnetics
An easy way to introduce magnetic parameters is to start with the difference between hard magnetics and soft magnetics. Hard magnetics are permanent magnets. Two parameters distinguish these materials: Their coercive field, Hc, which is the strength of the magnetic field necessary to remove their magnetization; and Mr, which is the magnetization in the material that remains after its removed from an external field. For permanent magnets, Hc is huge (greater than 1,000 A/m) and so is Mr. These two properties are what allow permanent magnets to magnetize other materials.
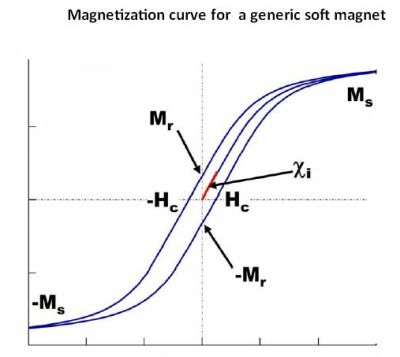
In contrast, inductive applications in power electronics need materials that have a low Hc and little Mr. The reason is that inductors in power circuits must be made of materials having a magnetization that will switch rapidly under the influence of a magnetic field created by current-carrying coils of wire. Soft magnets have these qualities.
Soft magnets have two other properties that are important for inductive applications. First, they have a high relative magnetic permeability, µr. Magnetic permeability is the ability of a material to support the formation of a magnetic field within itself. It is often expressed as the ratio of a material’s permeability to that of free space, µ0, so that µr = µ/ µ0.
The high µr of a soft magnet used in inductors concentrates the magnetic field lines inside the windings. It does so by orders of magnitude more than that of an air core. This concentration of magnetic field lines allows more storage of energy in the form of magnetic flux density.
Of course, it’s desirable to fabricate soft magnetic devices that can handle magnetic fields that are as high as possible. The maximum magnetic field a soft magnet can handle is a function of another parameter called Ms or saturation magnetization. This is the highest amount of magnetization the material can support.
Tradeoffs in soft magnets
Though soft magnetic cores boost energy density, they also are a source of energy loss, particularly as frequencies rise. A lot of the work going on in soft magnetic materials aims at reducing two kinds of losses, hysteretic and eddy current.
The first kind of energy loss to consider is that arising because of hysteresis. Every time a soft magnet is magnetized and demagnetized, it traces out a magnetization curve. The area inside the curve is a measure of the energy lost.
The property that gives rise to the magnetic hysteresis curve is magnetic coercivity. It is defined as the degree to which a material withstands an external magnetic field without becoming demagnetized. In other words, it is how much a material resists demagnetization. Coercivity can also be viewed as the intensity of the applied magnetic field necessary to reduce the magnetization of that material to zero after the material’s magnetization has been driven to saturation.
A point to note about the hysteresis curve is that it is traced out for each cycle of ac through the inductor. So there are hysteresis losses for every ac cycle. Thus even soft magnetics with a low coercivity (and a small hysteresis) can become lossy as operating frequencies rise.
A second major mechanism for losses in soft magnetics arises because of eddy currents. These are closed paths of electrical current generated in a conductor because of a time-varying magnetic field. These current loops create a magnetic field opposing the change in magnetic flux.
Power losses from eddy currents rise with the square of operating frequency. Thus they can be the main source of energy loss at high switching rates.
The losses arising due to the combination of hysteresis and eddy current losses are sometimes referred to as core losses, particularly in the context of electric motors. Core losses in electric motors don’t depend on the amount of the motor load. As outlined above, they depend on properties of the magnetic material, the flux density, and the switching frequency (which determines the rate of change of flux density). Estimates are that core losses account for about 25% of the total losses in conventional ac electric motors but are much higher for motors operating at higher rpm.
In power electronics, the most widely used soft magnetic material is ferrite. The good thing about ferrites is their high electrical conductivity (10 to 108 µΩ-m) which lets them keep eddy currents low. They are also relatively inexpensive to produce because they are made like ceramics.
A point to note is that there are both hard ferrites and soft ferrites. Hard ferrites have a high coercivity and are used to make ferrite magnets. Soft ferrites are what go into inductor cores. The most common soft ferrites are manganese-zinc ferrite and nickel-zinc ferrite. MnZn ferrites have magnetic permeability and saturation levels exceeding those of NiZn ferrites and generally find use at switching frequencies below 5 MHz. NiZn ferrites have a higher resistivity which makes them good candidates for applications above about 5 MHz.
Materials makers tweak the properties of ferrites by adjusting material composition and processing, adjusting factors such as temperature stability and magnetic permeability.
Another point to note is that soft ferrites are ferrimagnetic. Most other soft magnetic materials are ferromagnetic. The main difference between the two lies with their magnetic domains. In ferromagnetics, the vector sum of magnetic moments from all the domains results in what’s called a spontaneous magnetization that is zero.
In ferrimagnetics, the magnitude of the domain spins are such that there’s a non-zero spontaneous magnetization of the material. The difference between the two phenomenon generally isn’t particularly important unless you are studying material properties rather than applying magnetic material in real circuits. But the ferrimagnetic nature of ferrites gives them a relatively low Ms, typically 0.4 mA/m or less at room temperature. In addition, Ms in ferrites is more temperature sensitive than in ferromagnetic materials.
Their high conductivity and a constant µr that extends well into the megahertz frequencies will probably let ferrites continue to find use in applications involving both a low energy density and low magnetic polarization. Research into improving their performance includes engineering their grain boundaries and embedding them in special substrates.
Another class of soft magnetic material getting attention is that of amorphous alloys. More specifically, soft magnetic amorphous alloys generally consist of nanograins of ferromagnetic material embedded in an amorphous matrix (glass ceramic). This material usually comes in the form of thin (generally 5 to 50 µm) ribbons. The thin cross section is a function of the fabrication process which involves cooling the material too fast for it to form large crystals.
Amorphous soft magnetic material has a high conductivity. This and the thin layers that typically characterize its form factor keep eddy current losses low. There are a lot of applications for this material at frequencies up into the tens-of-kilohertz range. Some of the formulations of amorphous soft magnets use nickel and cobalt compounds to boost Ms and the Curie temperature of the amorphous and crystalline phases, thus allowing higher operating temperatures. Nickel is less expensive than cobalt, so it gets more attention among researchers.
One difficulty associated with amorphous material is that it is quite hard, so hard that it would rapidly wear out conventional cutting tools. Water-jet cutting, EDM, and grinding operations have all been used to shape amorphous magnetic cores. But all in all, amorphous materials tend not be used in situations demanding magnetic material with complicated geometries.
In inductor cores where the geometry isn’t complex, however, amorphous soft magnets can boost energy efficiency. The classic example is in cores for distribution transformers. Distribution transformers provide the final utility voltage step down, reducing the voltage in the distribution power lines to the level used by businesses and residences. Distribution transformers are energized 24/7 even when not powering a load, so it pays to minimize their core losses. Estimates are that about 10% of the distribution transformers in the U.S. now use amorphous magnetic cores.
Another class of soft magnetics is comprised of composite powders. Soft magnetic composites (SMCs) use micrometer-scale iron and iron alloys such as Fe-P, Fe-Si, and Fe-Co. Research is also underway in nanometer-sized SMCs though none are yet commercially available.
SMCs offer a potential energy savings because their composite structure can be manipulated to reduce losses during magnetic cycling. Embedding conductive magnetic particles in an insulating matrix boosts conductivity (10−3 to 10−1 µΩ-m) and reduces eddy current losses, although magnetic hysteresis losses rise. This increase in the coercive field arises because the particles retain some mechanical stresses. It’s thought that moving to nanometer-sized particles could make it easier to anneal away such stresses.
Use of magnetic composites also makes it possible to tune the material’s µr and, in turn, its magnetic saturation qualities. Usually, circuit designers try to avoid saturating inductive cores by limiting the applied current, reducing the number of windings, making the core bigger, or giving the core an air gap to reduce µr. It turns out that spacings of SMC nonmagnetic material in the direction of magnetization effectively make up distributed air gaps. Distributed gaps avoid the magnetic flux leakage that arises in a core with a discrete air gap; only a negligible magnetic flux extends beyond the core. Additionally, this sort of distributed air gap also promotes soft saturation; µr drops slowly as saturation approaches, making saturation less disruptive.
SMCs also have a relatively simple manufacturing process that involves mild forces and low temperatures. For example, an iron-powder SMC core typically goes through mild compaction and moderate heating of about 200°C for organic matrices and around 500°C for inorganic matrices. They can also be compacted into complex shapes without any extra machining. And their uniform physical make-up also lets composites suppress eddy currents equally in all directions.
Right now, there’s a great deal of interest in formulating SMCs with nanoparticles. One reason is that reducing the particle size would cut eddy current losses to negligible levels. The problem is that the physics at these nano dimensions get complicated. For example, hysteresis losses have a complex relationship to particle size. The stresses and surface defects in micrometer-scale materials make hysteresis worse and worse still as particles approach the size of a single magnetic domain.
The reason is single-domain particles do not reverse their magnetization via the usual means, by domain wall motion. Instead, it takes place through rotation of the magnetic moments within each particle. It takes a lot of energy to get this rotation in the largest single-domain particles. When the nanoparticles reach a critical size, generally in the tens of nanometers, there can be enough thermal energy to freely reorient the particle’s direction of magnetization. The temperature above which this is true is called the superparamagnetic blocking temperature. The particles no longer exhibit magnetic hysteresis and are referred to as superparamagnetic.
This situation sounds good from the standpoint of a core material; there’s no Hc and µr can be high. The weakness of the scheme is that there must be enough nonmagnetic matrix material to hold the individual nanoparticles apart. If magnetic nanoparticles come close together, they can magnetically couple and form ferromagnetic domains, leading to domain walls and magnetic hysteresis.
Researchers figure nanocomposite SMCs probably can’t be much more than 50% magnetic material. Still, the nanocomposite idea looks like a promising way of making materials with low losses.
Leave a Reply