High voltages and high currents circulating in EVs make the fundamentals of electrical isolation techniques an important topic.
Ross Sabolcik, Silicon Labs
AS automotive designs move toward electrification, high-wattage power electronics become critical to new electronic drivetrain and battery systems. In these applications, digital controllers safely interface with the high-voltage systems of modern electric vehicles thanks to galvanic isolation. Galvanic isolation is critical to the operation of these circuits, so it can be useful to review the basics of electrical isolation and how modern automotive electronics implement it.

Galvanic isolation refers to a means of preventing current flow between two parts of an electrical system. The key trait of galvanic isolation, compared to ohmic isolation, is that it has no direct conduction path between the two circuits. Put another way, the output power circuit is both electrically and physically isolated from the input power circuit. But galvanic isolation still allows energy or information to be exchanged between the two sections by other means.
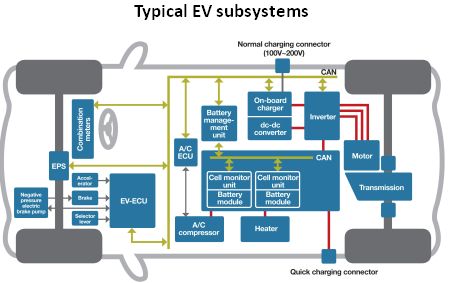
There are two main reasons galvanic isolation may be necessary. The first is that the electrical grounds of the two electrical systems may be at different potentials. In the absence of galvanic isolation, there can be ground loop current flowing between two units sharing a ground conductor. Ground-loop currents constitute electrical noise that can interfere with the operations of either circuit. Moreover, if the difference in ground potentials is sufficiently large, the resulting ground-loop current can pose a safety issue.
Thus the second reason for galvanic isolation is safe operation. Safety is the primary reason galvanic isolation is mandated in automotive electronics. EVs and mild hybrid electric vehicles (HEVs) are characterized by high-voltage circuitry carrying lethal currents. The high-voltage sections are under the control of digital electronics employing milliamp-level currents. Galvanic isolation, compared to other types of isolation, is a more robust way of preventing faults in power stages from damaging the control electronics that operates them.
High-voltage circuits in EVs
It is useful to review the high-power circuits found in EVs and HEVs. Both kinds of vehicles generally employ 48-V systems and batteries with high energy storage density and the ability to charge in minutes instead of hours. In addition, the battery management and associated power conversion system must be small and light weight, and they must “sip” battery current. Modern EV/HEV designs use modular components in the drive train and energy storage/conversion systems. EV/HEV battery management systems typically include five major circuit assemblies:

On-board charger (OBC): Lithium-Ion batteries get charged by an onboard charger consisting of an ac-to-dc converter with power factor correction that is supervised by a battery management system.
Battery management system (BMS): The BMS monitors and handles the charging and discharging of battery cells to ensure high efficiency and safety. Specifically, the BMS controls the charging, state of health, depth of discharge, and conditioning of individual battery cells.
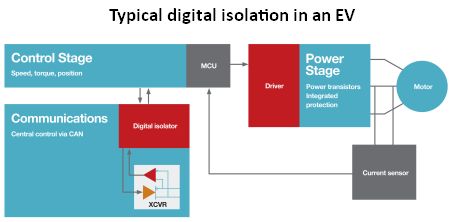
DC/DC converter: The dc/dc converter connects the high-voltage battery to the internal 12-V dc network, which also powers accessories and provides bias to the local switching converters.
Main Inverter: The main inverter drives the electric motor and is also used for regenerative braking and returning unused energy to the battery.
High-performance isolation protects digital controllers on the vehicle from voltages that can be well over 300 V. High-voltage subsystems, such as the OBC, are typically controlled over a CAN bus, which likewise must be isolated.
The low-voltage controllers in an EV communicate with high-voltage subsystems over connections that are often noisy because of proximity to high currents and electrical switching. In addition, low-voltage controllers must stay isolated from the high-voltage power transistors they control while also measuring the currents or voltages in other high-voltage sections of the system. Systems outside the EV, such as electric charging piles, have similar system requirements and needs for isolation.
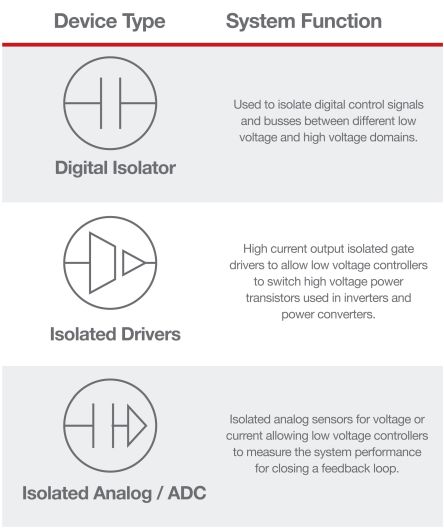
Several types of isolation technology can be used in electric vehicles including isolation transformers, optocouplers, capacitor-based semiconductor isolators, and transformer-based semiconductor isolators. Isolation transformers use magnetic fields to communicate across the isolation barrier with dielectric insulation between the windings and the magnetic core providing the isolation barrier. Optocouplers use an LED and optodetector to communicate across the isolation barrier. The airgap between the LED and photodetector is typically not wide enough to support the isolation voltages required. As a result, a dielectric tape is inserted between the devices in an optocoupler to increase the isolation rating.
Semiconductor-based isolation uses either a differential capacitor pair or a MEMS-based transformer as the isolation component. In these devices a signal is modulated across the barrier to pass information. In capacitor-based isolators, silicon dioxide is typically used as the dielectric. A polyimide layer is used in transformer-based systems. An isolation channel consists of a transmitter and receiver separated by this semiconductor-based isolation barrier. Modulation can be based on either an on-off keyed RF carrier or an edge-based detection scheme. The receiver contains a demodulator that decodes the input state according to its RF energy content.
The RF on/off keying scheme offers superior noise immunity compared to edge-based schemes but with the tradeoff of higher power consumption. Compared to optocouplers, semiconductor-based isolators have numerous advantages including longer lifetimes, significantly better stability over temperature and aging, faster switching, and much higher noise immunity.
Semiconductor-based isolation is particularly helpful as automotive suppliers target wide bandgap power transistors based on gallium nitride (GaN) or silicon carbide (SiC). GaN or SiC systems often use higher switching speeds to reduce the size of the system magnetics, a practice which can result in significantly higher electrical noise. Semiconductor isolation can deal with these higher speeds and noisier environments.
The shrinking the size and rising power density of automotive electronics will drive operating temperatures higher, which can stress optocouplers and reduce their performance. Semiconductor-based isolation has significantly better reliability over these higher temperature ranges, making them a good choice for EV designs.
Inside the OBC and BMS
It may be helpful to review applications in EV and HEV electronics where galvanic isolation based on RF techniques can be helpful. One area is in the OBC system responsible for converting a standard ac charging source into a dc voltage that charges the vehicle battery pack. In addition, the OBC performs other key functions such as voltage monitoring and protection.
The OBC system takes the ac input source, converts it to a high-voltage dc bus voltage using a full-wave rectifier and provides power factor correction (PFC). The resulting dc signal is chopped into a switched square wave that drives a transformer to create the required output dc voltage. The chopping of the input signal takes place using isolated-gate drivers such as Silicon Labs’ Si8239x device.
The output voltage can be filtered to the final dc voltage using sync field effect transistors (FETs) under the control of isolated-gate drivers. The output voltage can be monitored to provide closed-loop feedback to the system controller using isolated analog sensors such as Silicon Labs’ Si892x device.
The entire system can be monitored and controlled through an isolated CAN bus. The CAN bus is isolated with digital isolators with integrated dc/dc power converters such as Silicon Labs’ Si86xx and Si88xx isolators.
A review of a simplified BMS system also highlights the importance of signal and power isolation. In most EV subsystems, the CAN bus is isolated from the high voltages in that subsystem through digital isolation. Modern digital isolation requires a power supply on both sides of the isolator (the high-voltage domain and the low-voltage domain). This power supply can also be used to power other devices attached to the isolator such as a CAN bus transceiver.
Isolation in traction motor systems
Several critical isolated components work in the traction motor drive system. The traction motor in most electric vehicles will be an ac induction motor. To drive the motor, the traction motor controller must synthesize a variable ac waveform from the high-voltage dc rail from the battery pack.
These systems require isolated drivers between the motor controller and the power transistors. The isolation allows the low-voltage controller to safely switch the high-power transistors to create the ac waveform. In addition, there is likely an isolated CAN bus in the motor control system and some method to sense the current being driven to the motor for monitoring and controlling speed and torque.
Automotive electronics must meet more stringent testing and quality standards than those for industrial devices. Most automotive customers require the more stringent AECQ-100 qualification, ISO/TS16949 audit compliance, extended operating temperatures ranges (-40 to +125°C) and extremely low defect rates.
These enhanced requirements mean automotive electronics suppliers must take additional steps to ensure their components measure up. Additional quality controls at the wafer fab, device packaging and final assembly are required. True automotive-grade devices must be supported by quality systems and documentation such as the Part Production Approval Process (PPAP), International Material Data Systems (IMDS) and China Automotive Material Data Systems (CAMDS).
All in all, ever-increasing power densities in EV subsystems create demanding thermal and electrical noise conditions. Semiconductor-based isolation offers significant advantages over legacy optocoupler solutions. Automotive customers demand wider operating temperatures, higher quality, and more stringent documentation and systems than industrial customers. Electronics suppliers that can meet all these demands are poised to ride the coming EV wave.
Hi Ross Sabolcik,
In EV’s the isolation requirement between HV (AC& HV Battery) to LV (+12V) need to consider as Basic Isolation or Reinforced Isolation.
When OBC is in operation (earth was connected to vehicle chassis), I am assuming that consideration of basic isolation will be ok.
But earth was connected to vehicle chassis, will it be ok if I consider basic isolation between HV battery and +12V or do we need to consider reinforced isolation?.
@Ashok
ISO 6469-3.2 Clause 7.3 states:
Measures for protection on the occurrence of a first fault,
The protection under first fault conditions states that the following
protective measures should be applied:
• periodic or continuous monitoring of the insulation resistance
• double or reinforced insulation
• layer of barriers/enclosures in addition to the basic protection.
In EV two wheelers, when REESS is high voltage, all parts are galvanically isolated from each other and chassis also or galvanically connected each other and chassis