Power quality (PQ) surveys are used in data centers, hospitals, and industrial installations to improve uptime and equipment performance by identifying the root causes of power quality problems. When discussing PQ problems, three important considerations are the types of PQ problems, the sources of PQ problems, and the tools for identifying and measuring PQ problems.
Four common types of PQ problems include (Figure 1):
- Voltage transients are rapid high-energy disturbances in the line voltage. They typically last less than one cycle and cause a discontinuity in the waveform. A voltage transient can result in data corruption, equipment failure, or damage and cause interruptions to operations.
- Voltage sags and swells are voltage decreases or increases, causing the line voltage to deviate from nominal by more than ±15% and lasting from half a cycle to several seconds. Depending on the equipment’s sensitivity and the extent of the deviation, random malfunctions or complete equipment failures can result.
- Harmonic distortion can occur on the voltage and/or current waveforms. Excessive harmonic distortion can cause equipment to overheat or malfunction, resulting in the corruption or loss of data in computer-controlled devices.
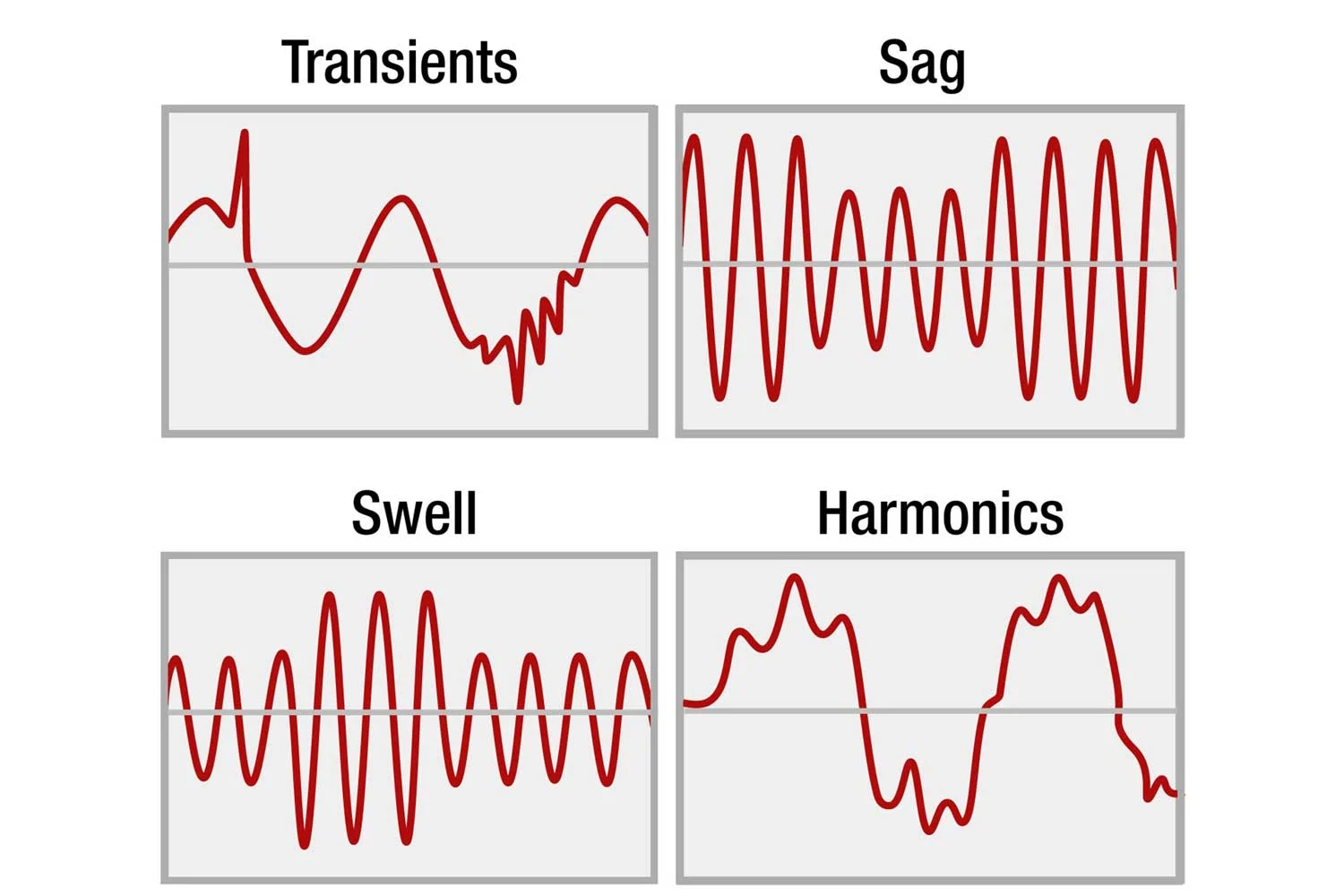
Other PQ issues can cause problems:
Interruptions are an obvious problem. They are the loss of power and can be momentary or sustained. Depending on the severity and other circumstances, the impact can range from interruption of operations to equipment damage and failure.
Voltage imbalances greater than ±2% on each leg of a three-phase power system are often a self-inflicted problem. They can occur when single-phase loads are unevenly distributed among the three phases. Poor connections or blown fuses can also cause voltage imbalances, which can result in erratic operation or equipment failure.
Low power factor (PF) (0.95 or lower) is another usually self-inflicted problem. It is caused when a circuit has highly inductive or capacitive loads like motors, lighting ballasts, and switching power converters that cause the voltage and current waveforms to be out of phase, resulting in the use of more apparent power than is needed.
Sources
PQ problems can arise from external and internal sources at a facility. External sources are usually utility-related. They can be caused by uncontrollable factors like lightning or utility operations, including PF equipment, switching operations, and various equipment faults, such as transformer or capacitor failures.
Internal sources are sometimes divided into two categories: general internal sources and power electronics sources (Figure 2). General internal sources include equipment like arc welders, certain types of medical equipment, and large motors directly connected to the AC line. Power electronic sources have traditionally included motor drives, large numbers of electronic power converters, etc. More recent additions to the power electronic list include smart grid, microgrid equipment, and electric vehicle chargers.
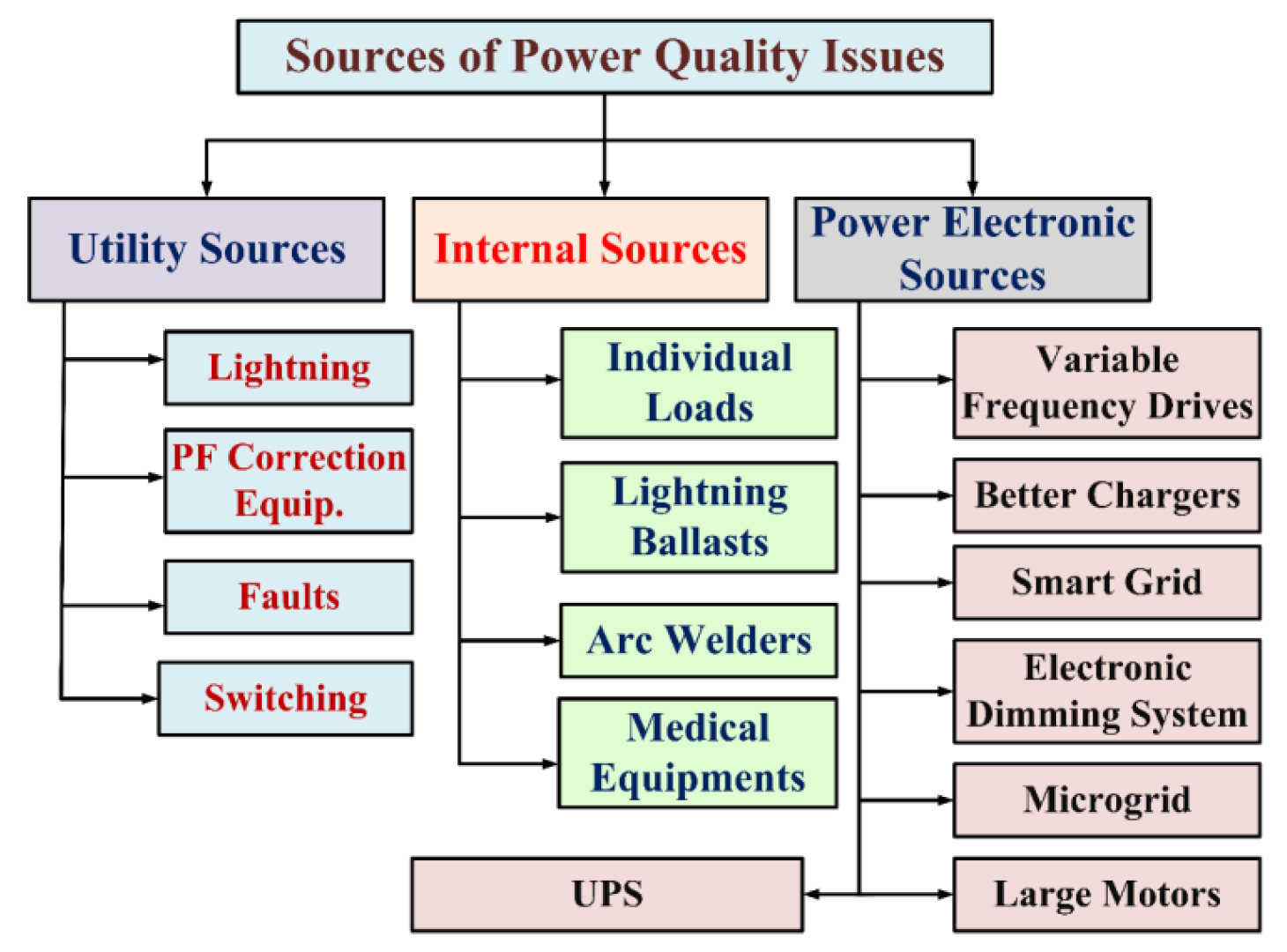
Tools
The two most common PQ tools are analyzers and loggers. These devices can monitor voltage, current, power (in watts and volt-amps), PF, etc. PQ analyzers provide continuous measurement and analysis of the performance of electricity lines to identify disturbances and other PQ problems in real-time.
PQ loggers, also called PQ recorders or energy loggers, measure and record various electrical parameters to help identify sources of PQ problems. Loggers are used to optimize operations and implement load studies for energy waste identification and PQ compliance monitoring.
Based on the operating environment and circumstances, there’s a wide range of PQ standards from various agencies, including ANSI/IEEE, NEMA, NFPA, NIST, IEC, UL, and other agencies. One common denominator for PQ analyzers and loggers is IEC 61000-4-30, “Testing and measurement techniques — Power quality measurement methods.”
Instruments certified to comply with IEC 61000-4-30 will produce reliable and repeatable measurement results regardless of the model or manufacturer. The standard establishes two classes for PQ measurement devices, Class A and Class S.
Class A (Advanced) instruments provide the highest levels of accuracy and precision and measure more parameters. They are used to verify compliance with the standard, resolve disputes, and meet other contractual and legal requirements. For example, the RMS value of the supply voltage must be measured over a continuous 10-period time interval. Measuring error may not exceed 0.1%.
Class S (Survey) instruments measure and log data and events more qualitatively with less stringent expectations for accuracy. Class A instruments are more comprehensive and include 8 required measurement parameters, while Class S devices are only needed to measure 5 parameters (Table 1).
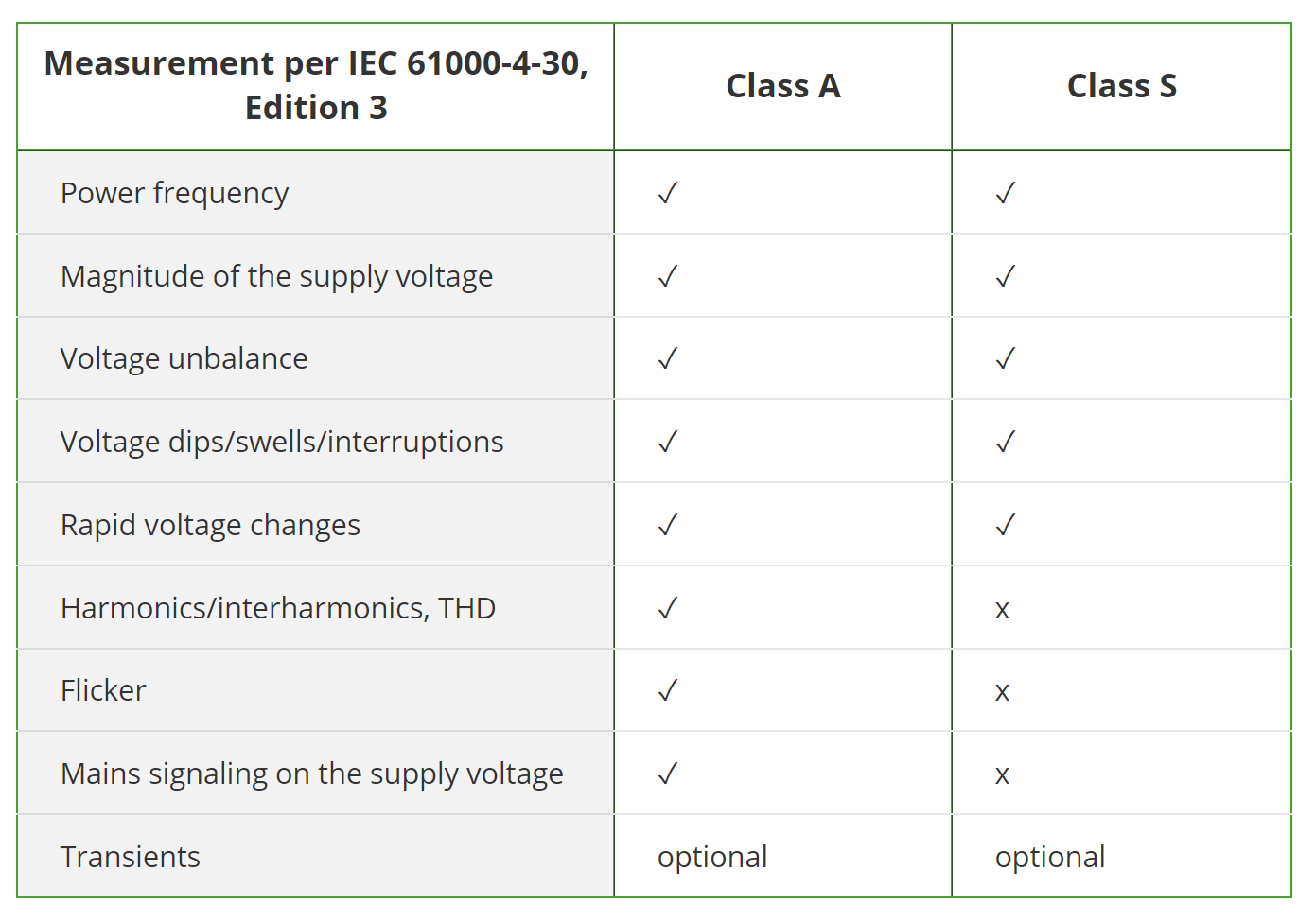
Summary
PQ surveys are used to identify the root cause of PQ problems and optimize equipment operations and availability in facilities like data centers, hospitals, and factories. They are also used for PQ compliance monitoring and dispute resolution.
References
4 Must-Know Tips for Conducting Power Quality Surveys, Hioki
Analysis and Mitigation of Power Quality Issues in Distributed Generation Systems Using Custom Power Devices, IEEE Access
Choosing the right equipment, Unipower
Power quality of commercial and industrial power systems, Hanover Insurance Group
Quick guide to power quality symptoms and causes, Fluke
The difference between Class A and Class S, Gossen Metrawatt
Leave a Reply