Radial flux AC motors offer some performance and packaging benefits but also bring some thermal and manufacturability issues.
Part 1 of this series examined the axial-flux motor (AFM) in detail and compared it to the very widely used radial-flux motor (RFM). Part 2 of this FAQ continued the exploration of AFMs and RFMs. This final part of the FAQ looks at some real-world issues associated with the adoption of AFMs.
Q: What factor may accelerate the take-up of AFMs?
A: There are several factors. First, there are applications such as EVs that could benefit from the performance and packaging of AFMs, such as EVs. Also, AFM design is greatly aided by new CAD/FEA tools for analysis of the EM field and flux paths, materials performance, error tolerance, thermal performance, and other considerations. New techniques, including the use of powered metals for fabricating the magnets, offer new production flexibility. Finally, there are new ways to assemble the needed parts and laminations of the non-winding parts of the motor.
Q: Are AFMs available in off-the-shelf units with standardized size, power, and performance as RFMs are?
A: No, they are not, but that may not be an impediment. High-volume potential applications such as EVs will require custom AFM designs which are highly optimized to meet their unique combination of requirements, and they will have the volume to support a custom design and fabrication. Many companies are working on innovative approaches to AFM design, claiming (or at least hoping) to offer a superior design from performance, manufacturing, and cost perspectives.
Q: Who are some of these providers of AFMs?
A: There are many start-ups and smaller vendors who are doing significant work in this area:
Mercedes-Benz claims that the AFM designed by their subsidiary YASA increases power density by more than 30% and delivers a 5% range benefit over RFMs that typically power mass-market EVs. A repurposed Mercedes-Benz factory in Berlin will build axial-flux motors for the automaker’s AMG electric-only platform. The main challenge will be to adapt the various manufacturing steps of assembly, production, and welding to the new design, and learn to handle the soft magnetic-composite materials they use.
Triaxial, a subsidiary of Belgium-based Magmax BV, has also developed AFMs that target EVs and e-mobility aircraft (e-taxis, small aircraft). They have a proprietary yokeless design that they claim is more efficient, lighter weight, and easier to manufacture.
Infinitum (Round Rock, TX) claims their innovative 10-horsepower AFM uses 66% less copper, has 50% of the size and weight, and uses 10% less energy than a comparable RFM motor. These are impressive claims, admittedly, for a smaller-horsepower motor.
In addition to offering motor-design CAD software, ECM PCB Stator Tech (Needham, MA) is developing a unique approach to the stator. Rather than using wound coils, they are investigating AFMs with stators using air-core, printed-circuit boards. ECM’s PCB Stators replace the copper windings found in conventional electric machines with an ultra-thin stator, this saving space and allowing more flexibility in design, optimization, and fabrication.
Note that established RFM manufacturers are not ignoring the challenges raised by AFMs. For example, Magnetic Innovations claims that their improvements to RFMs make them functionally competitive with AFMs while using existing low-cost manufacturing processes.
Q: Tesla is a major user of motors; what kind do they use, and are they AFMs?
A: Most Tesla EVs use a liquid-cooled AC permanent-magnet synchronous motor, with variable-frequency drive for the rear, and an AC induction motor, also liquid-cooled and with variable-frequency drive for the front drive. Neither motor is an AFM, although they are reportedly exploring their use.
AFMs might possibly allow the motor to be mounted in the wheel assembly itself which has some design and production advantages, but doing so also adds to unsprung weight, which degrades vehicle handling, ride comfort, and other control aspects.
Q: Finally, what is the electrical drive for an AFM compared to an RFM?
A: The same variable-frequency drive (VFD) electronics are used, but the drive algorithms are slightly re-tuned to mesh with the differences in performance. Early VFDs were all analog, but they have largely been made obsolete by processor-controlled digital ones. The VFD digitally creates a sine-like wave from a higher-frequency stream of pulses and pulse-width modulation (PWM) (Figure 1). The VFD also modulates ramp-up and ramp-down on power-on and off sequences to minimize inrush current, surges, vibration, and possible shock damage to the motor or its load.
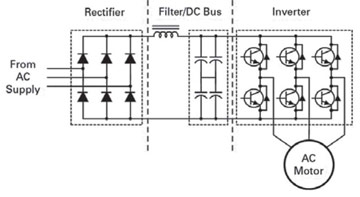
The VFD sets, controls, and changes the frequency of this sine wave according to what the motor is being called upon to do. An amplifier in the VFD then boosts this sine signal to the voltage and current needed to power the motor. The carrier frequency of a VFD is the frequency of the PWM switching and typically ranges from 2 kHz to 20 kHz.

This high-frequency PWM output is then used to create the lower-frequency sine wave and provides the variable frequency output to the motor; this frequency typically spans 0 Hz to 400 Hz. The physical size and packaging of a general-purpose VFD for fixed-in-place industrial applications ranges from a small box to a large cabinet, depending on the required voltage, current, and power level (Figure 2).
In contrast, the VFD drive for a specialty application such as an EV motor or motors will be a custom design with attributes and performance that are tightly matched to the specific RFM or AFM used as well as the many automotive safety and operating-environment mandates. In addition, the packaging will be designed to fit the available space and location in the vehicle as well as deal with the thermal issues and extreme temperatures of a vehicle.
EE World Related Content
Brushless motors and motor nameplates
Scope-based diagnosis of three-phase motor drives
Why you don’t need a variable-speed drive to change a fan’s speed
FAQ on traction motors, part 1
FAQ on traction motors, part 2
FAQ on traction motors, part 3
Unipolar vs. Bipolar drive for stepper motors, Part 1: principles
Unipolar vs. Bipolar drive for stepper motors, Part 2: Tradeoffs
Unipolar vs. Bipolar drive for stepper motors, Part 3: Drive ICs
FAQ on servo motors: part 1
FAQ on servo motors: part 2
External References
Iowa State University, “Motor Characteristics”
YASA, “Axial flux: The future of performance electric vehicle propulsion”
E-Mobility Engineering, “Axial flux motors”
Stanford Magnets, “An Overview of Axial Flux Motor & Axial Flux Motor Magnet”
Magnet Academy, National Mag Lab, “Davenport Motor – 1834”
Eaton, “Why torque density is important to machine design”
Horizon Technology, “Electric Motor Design: Radial vs. Axial & Transverse Flux”
Triaxial BV, “Axial Flux Motor vs Radial flux Motor: A Focus on Magnetic Field Orientation”
Triaxial BV, “Why Aren’t All Electric Vehicle Motors Axial Flux (Yet)?”
Magnetic Innovations, “What is a radial flux permanent magnet motor?”
Storables, “What Electric Motor Does Tesla Use?”
Tesla, “Subsystems: Motor Types and Specifications”
European Journal of Electrical Engineering, June 2014, “Magnetic Modeling of Radial-Flux and Axial-Flux Permanent-Magnet Motors for Direct Drive Automotive. Specifications and Comparison”
Oak Ridge National Laboratory, “A Comparison of Outer Rotor Radial and Axial Flux Machines for Application in Electric Vehicles”
Kilowatt Classroom LLC, “Variable Frequency Drive Fundamentals”
VFDS.org, “Variable Frequency Drives”
Leave a Reply