Ultrasonic sensing is used in various automotive and industrial applications ranging from liquid level sensing to robot obstacle detection and automated parking assistance. Transformer-based designs can produce highly accurate solutions with maximum ranging distances. This FAQ will review several applications for ultrasonic sensing, compare the capabilities of transformer drive with direct drive solutions, and then dive into some of the details related to transformers for ultrasonic sensing applications.
Ultrasonic sensing measures the time interval between when an ultrasonic signal is sent and reflected from an object. It’s a cost-effective solution for many short-distance (30 cm to 8 m) object detection needs. Common frequencies for the ultrasonic signal range from 40kHz to 200kHz, but higher and lower frequencies are also used for application-specific needs. Ultrasonic sensor technology continues to develop and improve. Automotive applications in automated driving and advanced driver assistance systems (ADAS) are rapidly growing. They include blind-spot warning presence and proximity detection, automated parking assist, kick-to-open, or smart trunk openers (STO) (Figure 1).
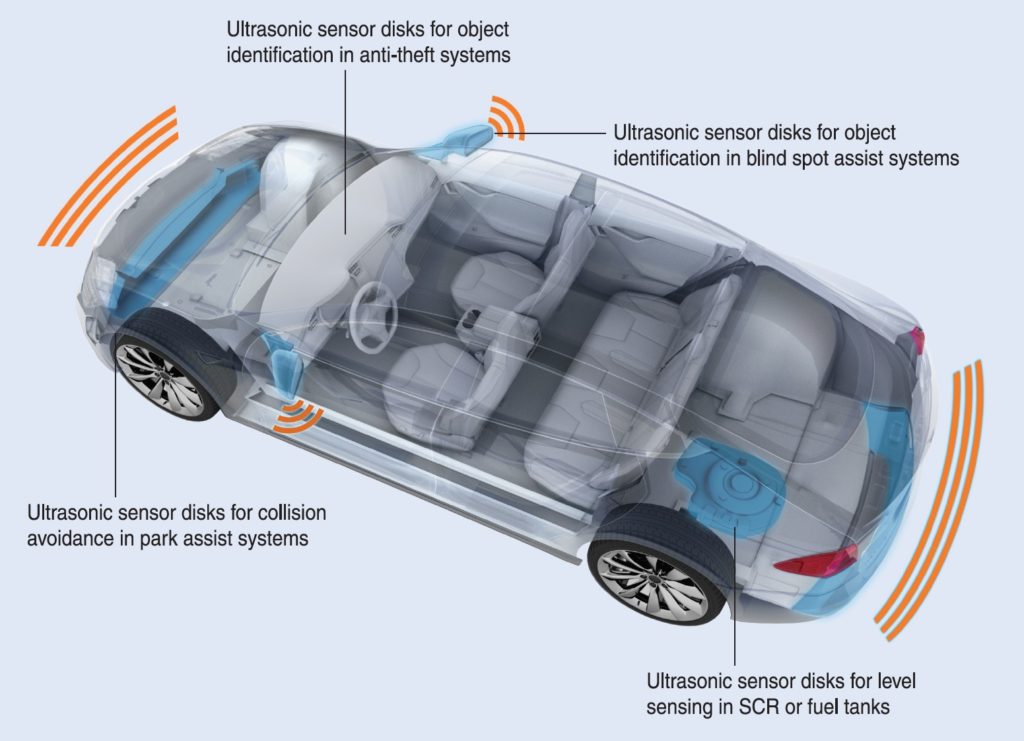
Many automotive applications using ultrasonic sensors can benefit from using a transformer-driven design (Figure 2). For example, parking assistance systems use multiple sensors on each bumper and need the added performance enabled by transformer-based designs. An electronic control unit (ECU) analyzes the inputs from the various ultrasonic sensors to identify potential obstacles and determine how far away they are. In these systems, transformers need to have tight inductance tolerances, including shielding from electromagnetic interference and very low drift across the automotive temperature range. These systems can have as many as 16 ultrasonic sensors placed around the car.
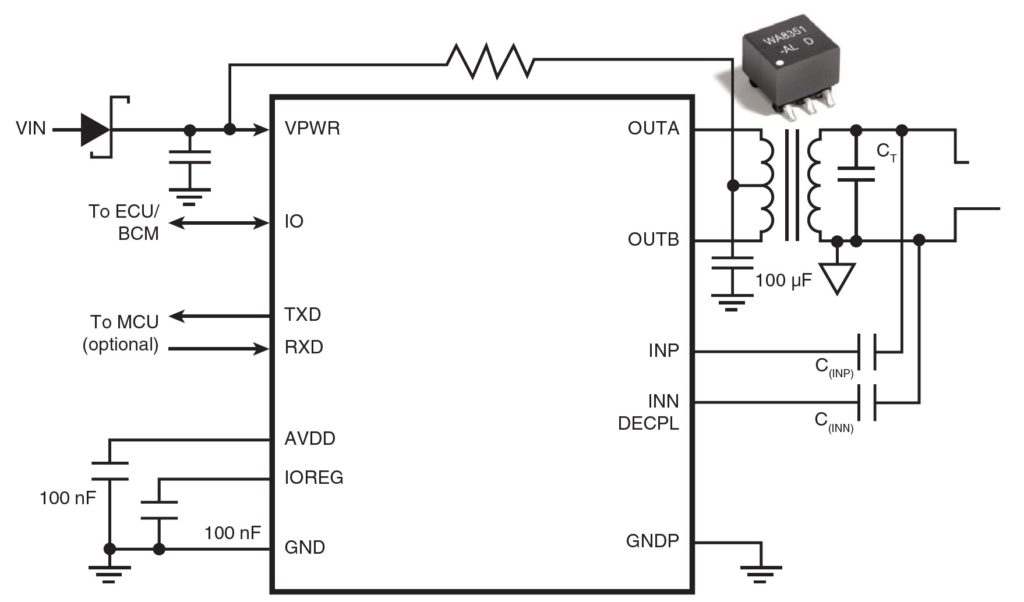
STO is an emerging application for ultrasonic sensors in cars. It enables people to open the trunk simply by waving (in a kicking-like motion) their foot near the rear bumper. Compared with capacitive sensing, ultrasonic sensing provides better sensitivity. And since this is a short-range sensing application, transformer-driven solutions are preferred because they can provide a more predictable ultrasonic ringing decay that results in more accurate short-range sensing.
In addition to transformer-driven solutions, some applications benefit from direct drive designs. Direct drive is simpler and lower cost but is limited in performance and is not usually found in automotive applications. Direct drive is used in cost-sensitive short-range applications with low-cost open-top transducers. When driving voltages are lower, using a half-bridge or full-bridge inverter can provide the AC drive voltage needed to excite the transducer. Transformer drive solutions provide higher performance and are typically used with closed-top transducers that operate at 80 V peak-to-peak (Vp-p) and higher voltages.
Ultrasonic boost transformers can be used to drive the transducer to the desired sound pressure level (SPL) (Figure 3). SPL is measured in decibels and is the logarithmic measure of the root-mean-square (RMS), or effective sound pressure of a sound relative to the threshold of a reference value. At the maximum specified transducer drive voltage, the transducer becomes saturated and cannot generate any additional SPL, and the SPL curve reaches its maximum level.
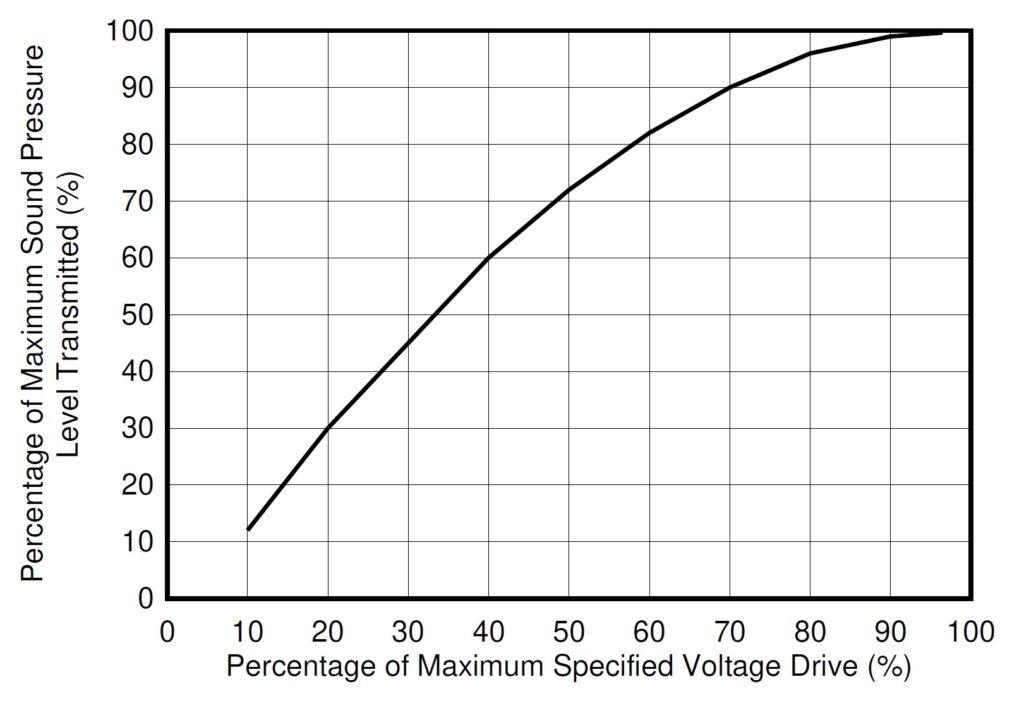
Transformer-driven systems combine the ability to accurately sense close objects by fine-tuning and reducing the transcoder decay ring time with the ability to support accurate longer-distance sensing. When sensing close-by objects, ring time is important. If it’s too long, the ringing can limit the ability to sense the reflected signal, resulting in missed objects or distance measurement errors.
The drive voltage is a key specification on ultrasonic ranging systems. There are many open- and closed-top transducer designs with drive voltages ranging from 5 to over 200 Vp-p. Especially for higher voltage designs, a transformer is needed to efficiently provide the sinusoidal or square-wave drive to the transducer at the required resonant frequency. A transformer-driven design also maximizes the SPL generated by the transducer without over-driving it for long-range measurements.
For drive voltages of about 80 Vp-p or higher, a single-ended or center-tapped transformer is often used with a turns ratio of 10:1, or higher. Typical input voltages range from 5 to 24 Vdc. Transformer drives can boost those relatively low input voltages to the higher levels needed for higher-performance applications.
Tunable-inductance transformers are found in some ultrasonic transducer drive designs. They have the disadvantage that the inductance can drift with temperature resulting in less than optimal drive performance or even unstable operation. Especially when operating over the automotive temperature range, the use of fixed inductance ultrasonic transformers can be beneficial. These transformers have a fixed and stable inductance up to an ambient temperature of TA = 125°C (Figure 4). Fixed inductance operation is important to support reliable and accurate distance measurements in automotive and industrial systems.
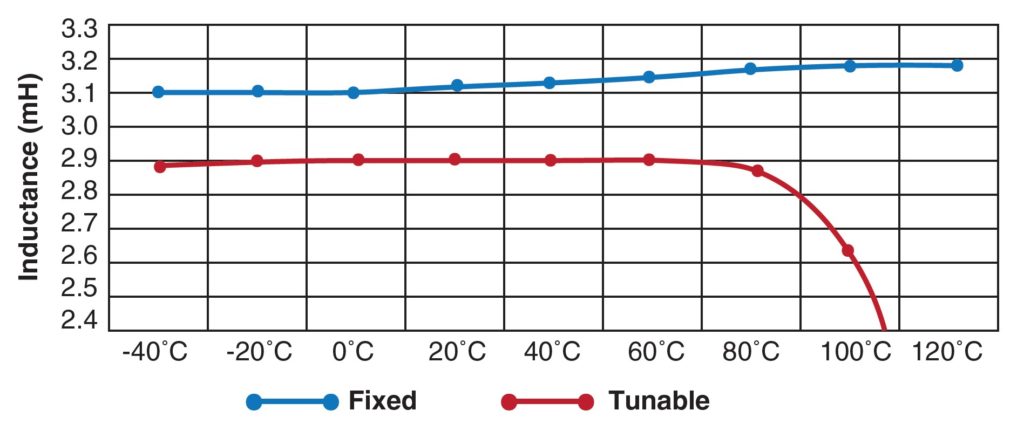
Mono-static vs. bi-static transducer architectures
Common ultrasonic transducer ranging system architectures can use a single ultrasonic transceiver (mono-static) or a separate ultrasonic transmitter and receiver (bi-static) (Figure 5). In more complex systems needing angular orientation, triangulation, and tracking, three or more transducers are used. The use of mono-static versus bi-static architectures involves tradeoffs between cost and performance. Mono-static architectures are generally the lowest-cost solutions but suffer from limited maximum detectable distances resulting from resonant effects and minimum detectable distances resulting from ringing. Separating the transmit and receive functions in a bi-static architecture improves system performance, especially for close-by object detection, where objects closer than a centimeter can be consistently detected.
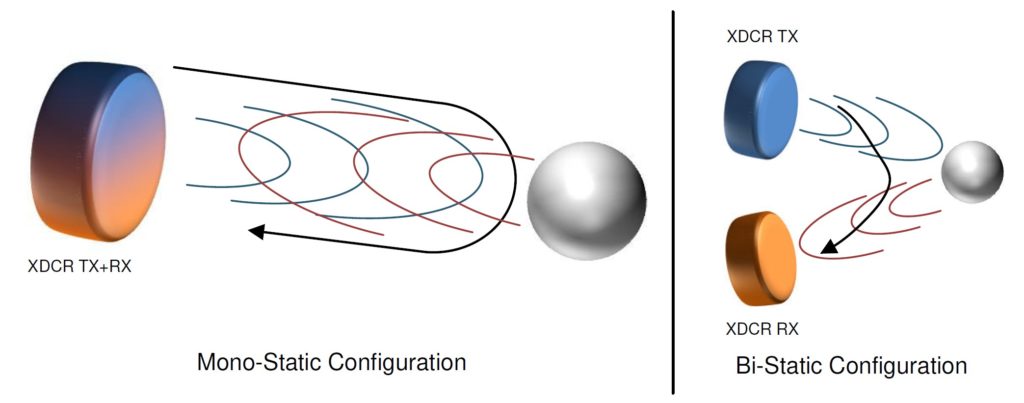
To improve the short-range capabilities of mono-static architectures, it is necessary to model the transformer and the transducer to minimize the effect of the ringing-decay time by adding a tuning capacitor (CTUNE) and a damping resistor (RDAMP) (Figure 6).
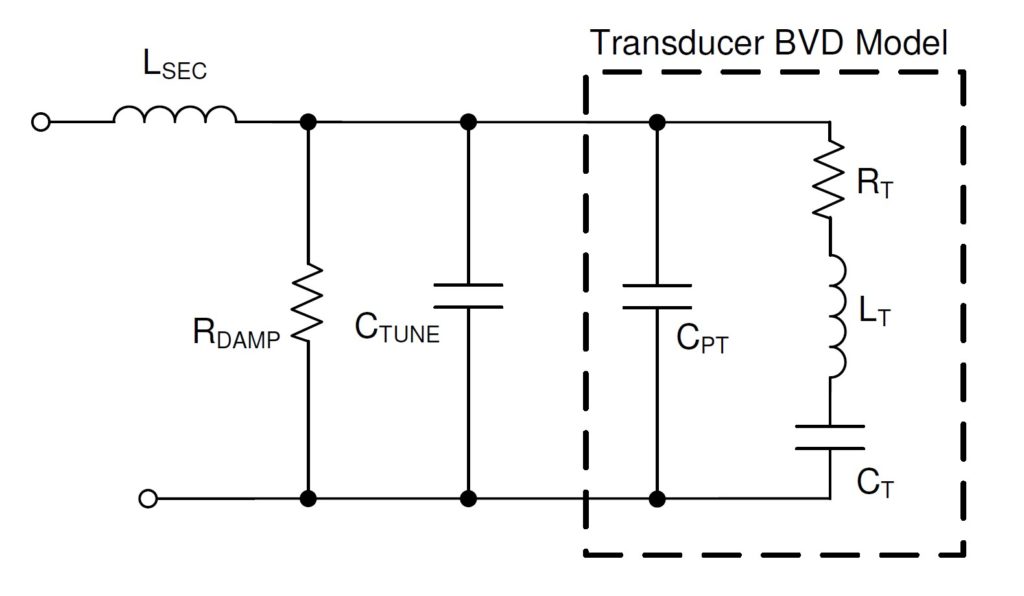
The transformer parasitics, especially the secondary-side leakage inductance (LSEC), need to be considered. Transducers are most efficient when resonating at their designed frequency. Any drift away from that optimal frequency results in a loss of SPL. When LSEC is added to the transducer Butterworth-Van Dyke (BVD) model, it impacts the transducer performance. There can be a mismatch between the driving frequency and the expected receiving frequency. Adding CTUNE in parallel with the transducer can match the LSEC of the transformer to the resonant frequency of the transducer. Values for CTUNE are usually between 100 and 2000 pF.
To reduce the ringing-decay time while maintaining drive power and long-range capability, RDAMP is added in parallel to the transducer. While the addition of CTUNE is not beneficial for bridge-driven topologies, the addition of RDAMP is beneficial in both transformer-driven and bridge-driven mono-static designs. Typical values for RDAMP can range from 500 Ω to 25 kΩ, depending on the circuit design and transducer characteristics.
Summary
Transformer-based designs can provide optimal performance across a wide range of industrial and automotive ultrasonic ranging and sensing applications. The transformers in these systems need to have tight inductance tolerances, include shielding from electromagnetic interference, and have very low drift across the automotive temperature range. In addition, designers need to consider transformer parasitics and the transducer BVD model to ensure optimal and reliable system operation.
References
Automotive Ultrasonic Sensing Module Reference Design for Park Assist, Texas Instruments
Investigation of the Half Bridge and Transformer Push–Pull Pulser Topologies for Ultrasonic Transducer Excitation, Journal of Circuits, Systems and Computers
PGA460 Ultrasonic Module Hardware and Software Optimization, Texas Instruments
Transformer Solutions for Ultrasonic Sensing, Coilcraft
Ultrasonic Sensor Disks For Automotive and Industrial Applications, TDK
Leave a Reply