Point-of-load converters (PoLs) are used in distributed power architectures (DPAs) to step down a relatively high power distribution bus voltage to the lower voltages needed by system components such as microprocessors, ASICs, and other digital ICs. DPAs are used in systems of all sizes to improve power distribution efficiency. Larger systems tend to use higher distribution voltages. In small portable systems, 5Vdc or 12Vdc are common, 48Vdc is often seen in data centers, and in larger installations such as large data centers or telecommunications central offices, 380Vdc is used. In the case of distribution voltages of 48V and above, the distribution voltage is stepped down to an intermediate voltage to power the PoLs, creating a two-stage power conversion chain.
The use of PoLs powered by an intermediate bus voltage is necessary because it is not efficient to directly convert 48Vdc or higher voltages directly to the very low voltages needed by today’s advanced digital ICs. In a typical PoL buck converter, the percentage of time that the power MOSFET is on during a switching cycle is called the duty cycle and is equal to the output voltage ratio to the input voltage. The step-down ratio from 48Vdc to 1Vdc, for example, is 48X. That would require an exceedingly small duty cycle resulting in inefficient use of the power MOSFETs and generally degraded performance.
PoLs typically operate with inputs of 5V (in portable systems) or 12V (in servers and other information technology and communications equipment), but are also used with inputs of 24V in some applications. These input voltages are stepped down to lower voltages, typically between 3.3V and 0.8V.
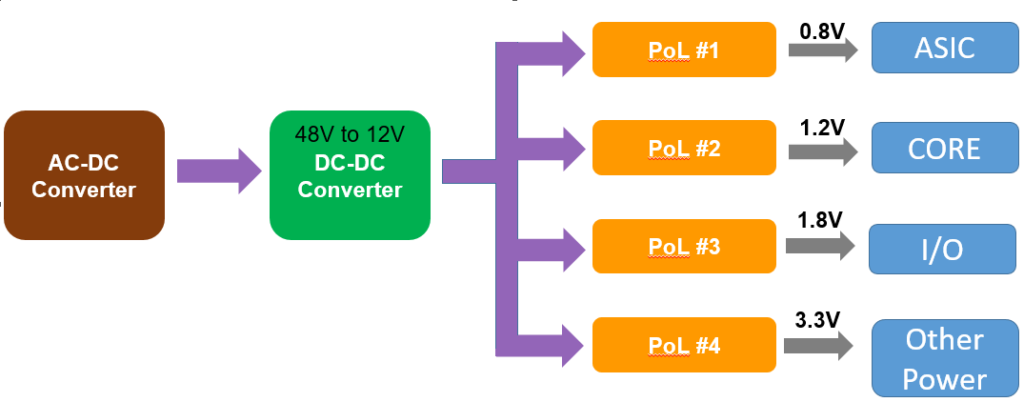
PoLs can be linear power supplies, such as linear regulators, or switch-mode power supplies, typically a buck topology. Switch-mode PoLs can be implemented using controllers, regulators, or complete modules. Distributed power architectures and PoLs are found across all application spaces, including IT, telecom, automotive, industrial, aerospace, etc.
Linear PoLs
Linear PoLs are typically low drop-out linear regulators (LDOs) and are the simplest PoL designs. LDOs lower voltages by dissipating power as heat. They are typically perceived to be less efficient than switching converters, but that’s not always the case. Depending on the operating conditions, LDO efficiency and power loss can compare favorably with a switching regulator. And LDOs are almost always lower in cost than switching regulators.
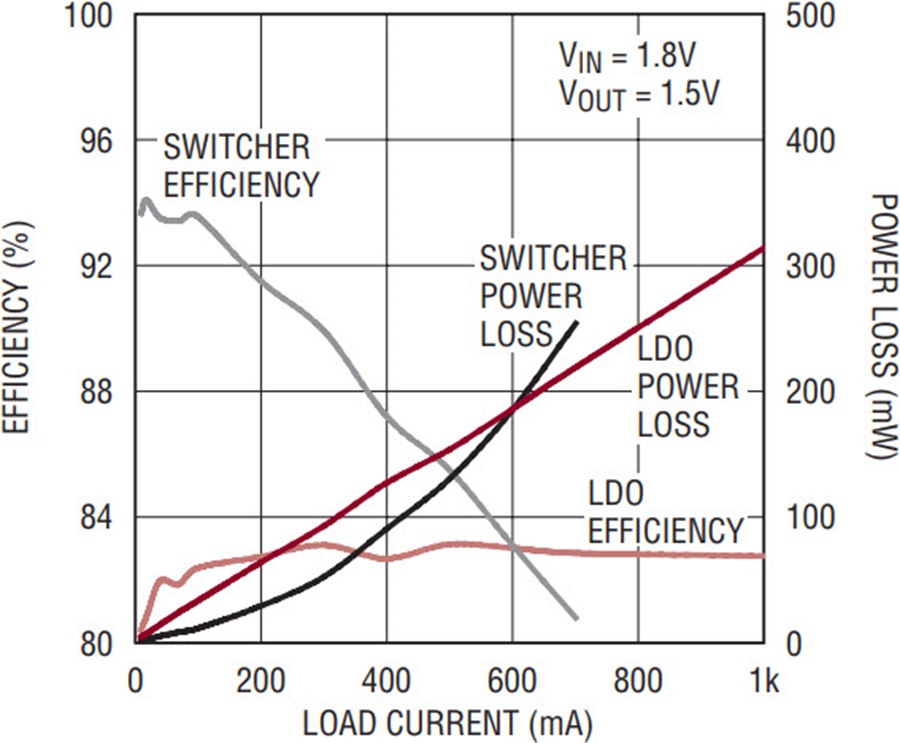
Factors other than efficiency can favor the use of linear regulators. For example, power supply rejection ratio (PSRR), also called power supply ripple rejection ratio or supply voltage rejection ratio (SVRR), measures how well a power converter blocks ripple from the input and prevents it from transferring to the output. PSRR is very important in radio frequency and wireless subsystems. For an LDO, PSRR measures the ratio of the output ripple relative to the input ripple over a wide frequency range, typically 10 Hz to 10 MHz.
Line transient response in LDOs is closely related to PSRR. The primary difference is that line transient response is a measure of the regulator’s response to large signals, while PSRR is based on small signals. These two specifications tend to be directly related: an LDO with superior PSRR will also have better line transient response characteristics. LDOs tend to be single ICs. Buck converters are more complex and are offered in a variety of integration levels and topologies.
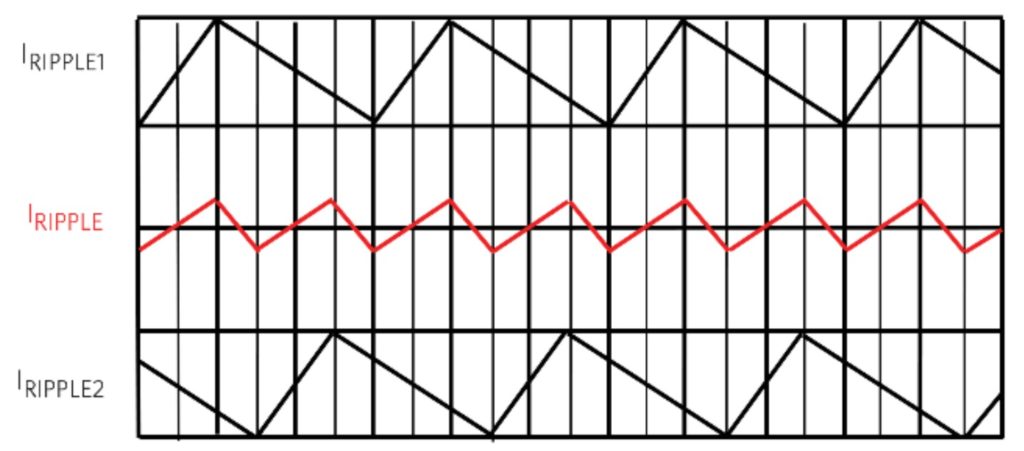
Buck converter PoL levels of integration
Buck converter PoLs can be categorized by three levels of integration; controllers, regulators, and modules:
- Controllers provide gate drives for external power MOSFETs connected through an LC filter to power the load.
- Regulators integrate the power MOSFETs with the gate drives, leaving the passive components outside the package.
- Modules bring the inductor (and sometimes the capacitors) inside the package and are the most integrated of the three solutions.
The selection of the “best” choice is driven by economics as much as it is by performance. In terms of component costs, controllers are usually the lowest cost solution but demand significant engineering resources, which can delay time-to-market. Designing compact high-frequency buck converters that achieve efficiencies in the range of 90% is not trivial. Circuit design needs are made more complex by the need to control layout parasitics. Specification of the output inductor is also a critical activity with many factors to consider, including DC and AC losses, magnetic core properties, avoiding saturation of the core, electromagnetic interference (EMI), and the tradeoff between power losses and device size.
Makers of regulators have control over the entire power train, which enables them to understand the filtering needs of the device in detail. As a result, regulators are often accompanied by recommendations of standard inductors that can be used to achieve specific performance levels.
Regulators usually result in smaller solutions compared with the use of controllers. Smaller solutions have several benefits; they tend to minimize EMI concerns. That can be especially important in systems with multiple PoLs. And regulators can simplify thermal management of the final design.
The inductor is typically the second most thermally dissipative component in a PoL; only the power MOSFETs dissipate more heat. Using an external inductor in a regulator-based solution can provide more flexibility in terms of thermal management. Modules, which bring the inductor into the package, can be more difficult to cool. The thermal derating curves for modules tend to require power derating at lower temperatures than those for regulator-based designs. That has the effect of limiting the operating temperature range of the PoL and reducing its effective power rating at typical operating temperatures. In some cases, PoL modules require power derating of 30% at an operating temperature of 65°C, while many regulators can deliver full-rated power up to 65°C.
Multi-phase PoLs
Controllers are typically used when designing multiphase PoLs. A single-phase buck PoL, whether based on a controller, regulator, or module approach, can efficiently deliver up to about 25A, but above that level, the use of a multiphase buck controller brings several benefits:
- Smaller output filter components can be used to meet the RMS ripple needs of the load.
- Efficiencies are higher.
- Transient performance is better.
- Thermal management can be simplified.
A multiphase PoL consists of a series of paralleled buck power stages (phases), each with its own inductor and power MOSFETs, driven by a single controller. The phases generally share input and output capacitors. The phases are interleaved, which means that they are switched at intervals equal to 360° / n throughout the switching period, where n is the total number of phases. Multiphase PoLs can have from 2 to 12 or more phases. The higher the needed load current, the more phases that are used. In addition, interleaving more phases effectively increases the operating frequency of the regulator.
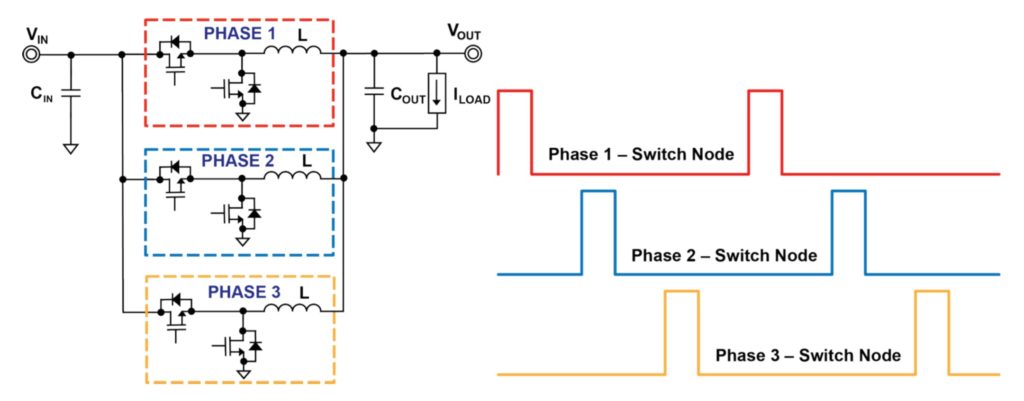
By spreading the current between phases, a multiphase design reduces hot spots. A two-phase buck PoL reduces the RMS current power dissipation in the FETs and inductors by half. Interleaving reduces transitional losses, and it reduces ripple currents at the input and output.
The reduced current in each of the phases reduces the output filter needs. For example, for a load needing 40A, a two-phase PoL will have an average current of 20A in each inductor. The lower average current and lower saturation current enables less inductance and a much smaller inductor than a single-phase design supporting the same 40A load.
As illustrated below, even with just two phases, there is significant ripple current cancellation in the output filter and a reduced ripple voltage across the output capacitors compared with a single-phase solution.
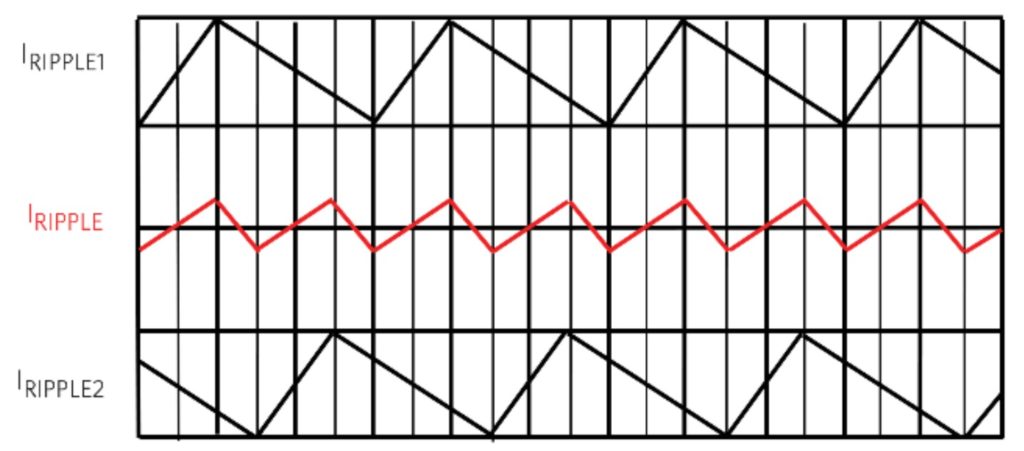
Load transient response is faster due to the reduction of energy stored in each output inductor. Current cancellation results in reduced ripple voltage and also helps transient response overshoot and undershoot. As more phases are added, these effects become magnified.
Summary
Implementation of distributed power architectures to increase power system efficiency requires PoLs as the final link in the power conversion chain to deliver well-regulated voltages to advanced digital ICs such as microprocessors, ASICs, and FPGAs. Designers have several technology choices when considering PoLs, including the use of LDOs versus buck regulators. Buck PoLs can be implemented with controllers, regulators, or complete power conversion modules. In applications that need more than about 25A, multiphase PoLs are used to improve system performance and manage solution size and cost.
References
How can a low-noise power supply be created using an LDO regulator?, Toshiba Electronic Devices
Integrated inductors empower multiphase buck converters for computing, Eton
LDO Linear Regulators Rival Switchers for Efficiency, Analog Devices
Multiphase Buck Design from Start to Finish, Texas Instruments
Optimizing the integration of point-of-load buck converters, Vicor
Understanding power supply ripple rejection in linear regulators, Texas Instruments
Understand the Multiphase Buck Voltage Regulator Advantage, Maxim Integrated
Leave a Reply