Induction heating is widely used in industry and even consumer appliances as a contact-free heating technique with many distinct advantages.
A very common design challenge for many engineers is to manage and dissipate excess heat produced within or impinging on a system so the temperature of that system or some of its components does not exceed some specified limit. However, there are designs for which the engineering objective is to create heat – often, lots of it – and deliver that heat to a load.
There are several ways to generate heat and convey it from that source to the load via some varying combination of the classic heat-energy transfer modes of convection, conduction, and radiation (Figure 1).
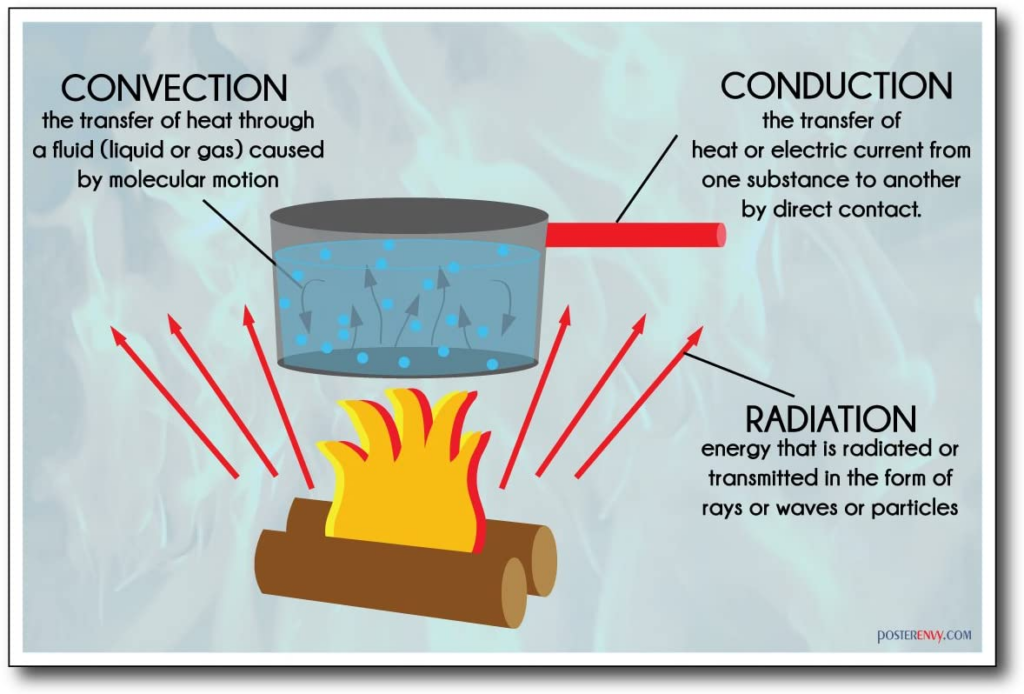
The historic and obvious way is to use an open flame (fired by wood, coal, oil, gas, or other fuel), but this has low efficiency and obvious physical-arrangement safety concerns. Another way is entirely electrical, by employing electrical resistive loss – usually considered a bad thing – into a heat source. With either of these approaches, the heat created must be directed to flow to the load.
An indirect approach is to use microwave energy to stimulate the vibration of molecules in the load and create heat but are not suitable for use with many types of materials, especially those that are electrically conductive. Also, the microwave energy must be confined in an RF-shielded enclosure for user safety, as microwaves can have adverse effects on living cells and tissues, as well as on inanimate materials.
There is still another approach that seems to be almost “magical” at first: induction (or inductive) heating. This is based on electromagnetic principles and the classic AC transformer first investigated by Michael Faraday in the 1830s, before electronics and even basic electricity as we know them were even established ideas.
Induction heating uses loss induced by the flow of magnetic energy rather than resistive loss due to the flow of electrical current to create heat in a targeted load. Unlike resistive-based heating, where the heat is created at the source and then conveyed to the load by some varying combination of conduction, convection, and radiation, the induction-created heat is created at the load itself.
This is done via the interaction of an alternating current (AC), which develops a magnetic field that, in turn, interacts with the vessel in which the load (material) to be heated is placed or the material itself. Induction heating is yet another case of clever engineering where a normally negative attribute – in this case, resistance and loss – is turned to positive use.
This article will look at the principles and applications of induction heating. Due to its many favorable characteristics such as non-contact approach, cleanliness, relative safety, and controllability, it is often used in commercial and industrial settings for basic heating but also melting large quantities of metallic substances.
It is also used in material test systems to heat a metal sample (Figure 2). I have seen induction heating in action, taking a solid steel test-sample rod about 5 cm long and 1 cm in diameter to glowing cherry red in a few seconds – that’s a dramatic demonstration you don’t forget.
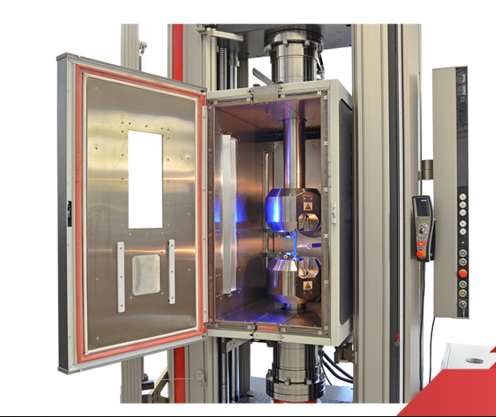
Induction heating is not a new development. As noted earlier, it began with Michael Faraday and his study of the induction of currents in wires by a battery being switched on and off – a crude way of creating a non-DC current flow (Figure 3). The fundamental principles of induction heating were later established and developed by James C. Maxwell in his unified theory of electromagnetism, while James P. Joule was the first to describe the heating effect of a current flowing through a conductive material.
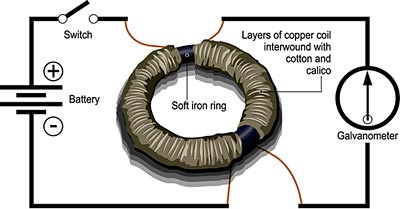
In 1887, Sebastian Z. de Ferranti proposed induction heating for metal melting and filed the first patent on the industrial applications of induction heating. The first fully-functional induction furnace was presented in 1891 by F. A. Edwin F. Northrup implemented Kjellin and the first high-frequency furnace application of induction heating in 1916.
Some consumers are familiar with induction heating, if not the principles, as it is used in some home stove-top ranges. Induction heating finds applications in processes where temperatures are as low as 100⁰C (212°F) and as high as 3000⁰C (>5400°F). It is used in short “flash” heating processes lasting for less than a second as well as in long-term heating processes that extend over several months.
The next part of this article will look at the principles of induction heating.
Related EE World Content
- Using Faraday’s Law of Induction
- Reverse-conducting IGBT targets induction heating apps
- What advanced sensing techniques are used to find lost treasures? Part 2: Electromagnetic induction
- IGBTs Reduce Cost in Induction Cooking Designs
- Basics of induction
- AC challenges with inductors
Additional References
Professional and Industrial References
- Wikipedia, “Induction heating”
- AZO Materials, “What is Induction Heating and How do Induction Coils Work?”
- GH Induction Atmospheres, “What Is Induction Heating?”
- Inductoheat, “What is Induction Heating?”
- RDO Induction LLC, “Fundamentals of Induction Heating”
- UltraFlex Power Technologies, “How Induction Heating Works”
- Wikipedia, “Royer Oscillator”
Consumer Use References
- Wikipedia, “Induction Cooking” (has efficiency numbers)
- Consumer Reports, “Pros and Cons of Induction Cooktops and Ranges”
- Martha Stewart, “The Pros and Cons of Induction Cooking”
- Don’s Appliances, “Induction Cooking: What is it and How Does it Work?”
- CDA, “How does induction cooking work?”
Do-It-Yourself References
- Homemade Circuits, “2 Simple Induction Heater Circuits – Hot Plate Cookers”
- Homemade Circuits, “How to Design an Induction Heater Circuit”
- Innovation Discoveries, “How to build and induction heater and how does it work?”
- RM Cybernetics, “How Does Induction Heating Work?”
- Autodesk/Instructables, “DIY Powerful Induction Heater”
Leave a Reply