The primary goal of EV protective circuits: Keep vehicle occupants safe day-to-day and first-responders protected if the worst happens.
Michael Zimmermann, Littelfuse, Inc.
The 12-V automotive battery may become a relic of the past as electric vehicles (EV) and hybrid cars gain market share. EVs and hybrid vehicles use battery packs of at least 500-V and some reach 1,000 V. The higher voltages are required to power electric drive motors efficiently. However, the potential danger to vehicle occupants—or to anyone who comes in contact with a vehicle—is more significant when high voltages are present.
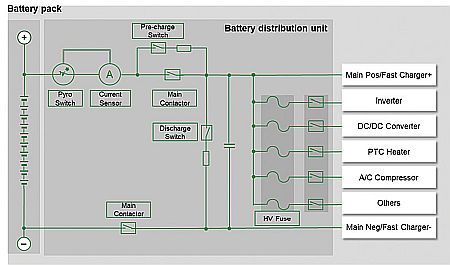
The high reactivity of metal lithium has brought considerable attention to battery safety. A battery management system (BMS) is necessary to safely operate a lithium-ion battery. The BMS monitors at least the state of each cell’s voltage and temperature and controls the equalizing currents, ensuring all battery cells connected in series have the same voltage. Highly developed systems also enable continuous monitoring of individual cell state-of-charge through permanent analysis of the energy flow during charging and discharging. In particular, high-performance lithium-ion batteries can see high short-circuit currents initially because thee batteries have a low internal resistance.
Lithium-ion batteries’ prospective (unaffected) short-circuit current is several times (about 5 to 10 times) that of other batteries, e.g., lead-acid batteries. The high value also makes the magnitude of the short-circuit current rise much faster than in conventional batteries because the electrical time constants are about the same – in the range of milliseconds.
To keep individuals safe from a short circuit and high voltage in an EV or hybrid vehicle, the primary requirements are disconnecting the high voltage energy sources from all loads and discharging any stored high voltage. Designers can design their circuitry to take three actions that will protect individuals from the energy that can short to the vehicle body through a load circuit failure:
Disconnect the battery from the load circuits to de-energize them.
Provide a high-speed disconnect method for the battery that energizes in the event of a catastrophic failure like a hard battery short circuit.
Discharge high-voltage capacitors and related energized systems to ensure safe voltage discharge.
In many cases, circuit breakers with magnetic or thermal overcurrent detection are too slow. Disconnection takes place only after a high battery discharge current is already flowing, and the circuit breaker is overloaded and may be damaged by high energy.
DC-capable fuses can serve as short-circuit protection but must be replaced once the source of the short-circuit has been found. In many cases, lengthy replacement times are impractical, and the fuse design is challenging. Still, fuses are the most reliable way to prevent catastrophic failure and enable a higher safety level. Companies like Littelfuse offer application engineering support and a wide range of fuse products for voltages ranging from 500 V to 1,000 V. For example, the Littelfuse 828 cartridge fuses and EV1K semiconductor fuses can handle up to 1,000 V.
In principle, many power electronic components are fast enough to switch the current off before it reaches critically high values in the event of a short circuit. However, these components have a comparatively small I²t value. (As a quick review, I²t is an expression of the available thermal energy resulting from current flow.) It is practically impossible to realize selective short-circuit clearing in a dc network with devices have a small I²t value.
The interruption of high dc currents—not easy in any case—has gained new emphasis with the adoption of powerful lithium-ion batteries. Ordinary dc protective devices usually don’t do the job here. Automotive standards require that EV and hybrid vehicle circuitry prevent a battery pack failure from damaging the vehicle and its controls.
In addition, electronics engineers realize their designs must protect people in the event of an accident. Any kind of accident could result in damage to the vehicle electronics. For example, an inadvertent connection between a high-voltage battery bus line and the metal exterior of a vehicle can cause a fatal electric shock. First responders as well as vehicle occupants would be at risk here.
Such scenarios show why it is necessary to disconnect the battery from load circuits when there is a catastrophic failure. Anticipating such conditions, designers should ensure high-power circuits have incorporated fast overload protection. The battery can deliver, almost instantaneously, potentially up to 30 kA during a short-circuit failure. High-voltage fuses have current interrupt ratings below 30 kA and an opening time of up to 50 msec. Consequently, they can’t open fast enough to prevent the massive current rise and protect against potentially irreparable damage. The battery distribution unit needs a better solution, which is a pyro switch.
High-speed circuit interruption
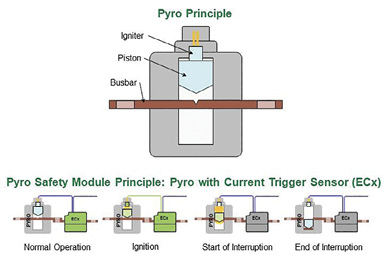
A pyro switch is a protection component capable of interrupting 30 kA of current from a high voltage source in under 1 msec. A current sensor detects the current overload and triggers the pyro switch to break the busbar connection in the battery supply line. The current detector’s signal activates an igniter that produces a high-pressure gas that moves a piston down on the busbar. The gas pressure is high enough to cause the piston to punch a hole in the busbar. The hole diameter is sufficient in size so the arc, caused by the breaking of the busbar, is extinguished.
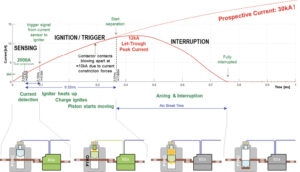
In a battery distribution unit, contactors connect and disconnect the battery during normal operation. The pyro switch and the current sensor sit close to the battery pack to detect a current overload and break the bus bar supply line in the event of a catastrophic failure. The loads have individual contactors and fuses for control and overcurrent protection. A discharge circuit removes voltage from high-voltage capacitors in the electronic sub-systems. When selecting a pyro switch and current sensing unit, consider selecting a pair with:
A voltage rating higher than the voltage of the battery pack
A modular package containing a current sensor and a controller circuit to save space and economy
An internal resistance under 100 µΩ to minimize power consumption during regular operation
An option for including a fuse in the assembly for protecting loads from minor overload current failures
CAN-Bus interface to communicate the state of the battery pack
For more protection, designers can add fuses in the battery distribution circuit. Fuses can protect against overcurrents during overloads that do not lead to catastrophic surge currents. Fuses can also protect EV wire harnesses and the charging cable. Fuses used in this circuit must have ratings that exceed the battery voltage. Consider using fuses that have:
A voltage rating of 500 V or, if required, 1,000 V
At least a 10 kA interrupt rating at 1,000 V for lower-rated fuses up to 30 A
Up to 30 kA interrupt rating for higher rated fuses
Nominal resistance under 10 mΩ
At least an opening gate of 500% of the rating, depending on the protection needs.
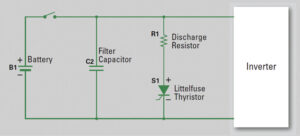
Filter capacitors across the battery will charge up to the battery pack voltage. An accident and the disconnection of charged capacitors from the main battery can still cause high voltages in the system. So designers should provide a means of discharging these capacitors. The discharge-switch circuit must handle high load currents and an occasional overload. The discharging function must stay operational over a wide range of environmental conditions during the vehicle’s life. Also, the discharge function should activate via a simple trigger control signal.
Consider using a thyristor-resistor discharge circuit across the high voltage capacitors. Resistor values should be such that they control the peak discharge current and have a low RC time constant for a fast discharge time.
Thyristors can provide a high surge capacity, superior heat dissipation, and better mechanical durability than MOSFETs or IGBTs. Furthermore, thyristors have a failure mode in which they short out under certain surge conditions, allowing a capacitor to discharge even if the thyristor has failed. Look for thyristors with:
Current surge capacity of 500 A or greater
An on-state current of 25 A or greater
Voltage rating greater than 500 V
AEC-Q101 qualification.
The top priority for those who design EV and hybrid electronics must be the safety of vehicle occupants and the personnel assisting with an accident. Designers can save precious development time by consulting protection component application engineers. They can assist with component selection and provide guidance on standards compliance. Also, some manufacturers offer pre-compliance testing to save time and minimize the cost for product certification.
Leave a Reply