Using energy harvesting and a rechargeable battery to power a remote wireless IoT node seems like an obvious and straightforward solution, but there are some unique aspects to consider.
Don’t get me wrong: I really like rechargeable batteries; in fact, I like them a lot. Whether based on lead-acid, nickel-cadmium, lithium-ion, or other chemistry, our modern lifestyle – from smartphones to electric vehicles and more – would not be feasible without them. I don’t need to elaborate for you about the usefulness and freedom they provide.
So, when the project requirement is to build a low-power, wireless IoT (Internet of Things) sensor to monitor a physical variable such as temperature or pressure in a remote setting far from any power line, it’s easy to decide on a strategy for powering the sensor-based device quickly. Just set up some harvesting scheme using ambient energy from light, vibration, RF, or thermal differential (to cite a few options), add a small rechargeable battery plus one of the many available power-management ICs, and the problem is solved (Figure 1).
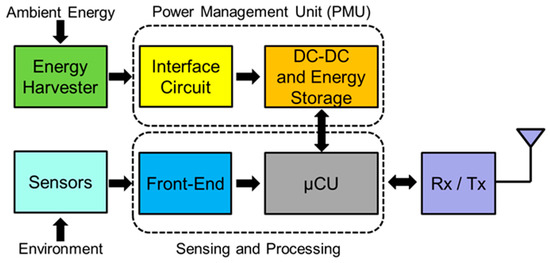
But in many cases, that’s short-sighted thinking with a jump to a conclusion. In practice, rechargeable batteries have their own idiosyncrasies and limitations. One of these, which is most easily overlooked, is the number of charge/disengage cycles they can endure before their energy-storage capacity drops by a significant amount.
How many cycles is that? It depends on many factors, but a good first estimate is between 500 and 1000 cycles under ideal conditions. If your system uses daily solar charging, you’re looking at between two and four years.
But “ideal” is not reality. The actual number of cycles is a function of how fully/deeply the battery is charged/discharged in each cycle, the rate of charge/discharge, the ambient temperature, and even the quality of the battery (shhh…). For most Li-ion rechargeable batteries, a general rule (with many exceptions) is that charging to 80 percent of capacity and discharging down to 20 percent yields the maximum number of cycles which is, obviously, a tradeoff against usable capacity.
Then there’s the issue of battery quality. As with most products, there are “better” and “lesser” versions of a given component. You can’t judge the battery quality by looking at its label or making basic measurements, as the factors which determine the performance (materials, manufacturing) are very hard to discern.
A further complication is that even if you specify a higher-quality rechargeable battery from a solid vendor and with the necessary performance, you never know what substitutions will be made by purchasing when offered a better deal. Even worse, there are lots of counterfeits and knockoffs of those better batteries in the supply chain (that’s another “shhh…), so even if you follow the rules and put your chosen vendor on the BOM purchase list with a “no substitution” tag, you could be surprised.
Consider other options
For these and other reasons, designers should also consider supercapacitors (formally known as electrical double-layer capacitors, or EDLCs) as alternate rechargeable energy-storage devices. They have different attributes compared to rechargeable batteries, and whether these are advantages or disadvantages depends on the application (Figure 2 and Figure 3).
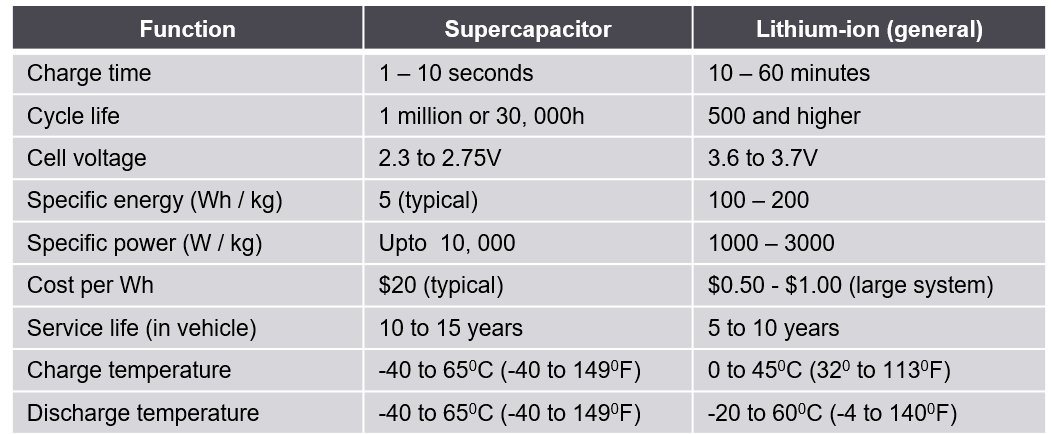
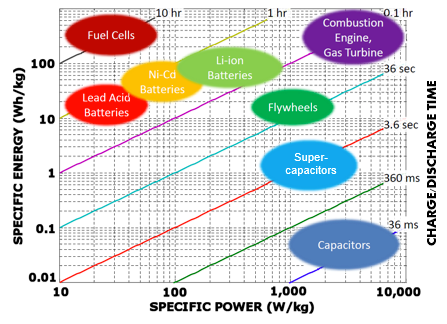
A way to get the best of both the rechargeable battery and supercapacitor attributes is to consider using both with appropriate charge/discharge management. This can be done by using one of each with appropriate management. Still, there’s another fairly new option from vendors such as Kemet and Taiyo Yuden: the lithium-ion hybrid capacitor.
This component is not just a repackaging of two disparate functions in a common enclosure. Instead, it is a complete re-design of both the rechargeable lithium battery and the supercapacitor from a fundamental materials and chemistry perspective, thus creating an entirely new component which has the characteristics of both.
Finally, there is another factor about energy harvesting that is hard to quantify. The energy source you expect to have available to harvest may not always be there. Sure, the Sun will be there, but will it be able to illuminate that PV cell? Tree grow, buildings are built, and people move things; the same long-term concerns apply to other harvestable energy sources. In short, the physical situation of the harvesting transducer may change over time through human or natural actions. Further, the harvester transducer may have a limited life as well; it could develop microcracks due to constant vibration or shock and eventually fracture.
Sometimes, you really have to step back and do a broad reassessment of the situation. While rechargeable power sources seem attractive – and they certainly are in many cases – sometimes a non-rechargeable, long-life Li-ion battery is a more reliable solution.
You can’t use just any Li-ion battery here, even a “better” one. Standard high-performance bobbin-type lithium thionyl chloride (LiSOCl2) batteries have a self-discharge of around 3 percent per year, regardless of load – even with no load. After 30 years, these batteries will have exhausted up to 90% of their original capacity. After you factor in the average annual current used to operate the wireless device, these batteries can fall below their threshold for usable capacity in less than ten years.
Fortunately, there is an alternative here as well. Vendors such as Tadiran offer non-rechargeable LiSOCl2 batteries, which, due to their material and manufacturing process, have an annual self-discharge rate of 0.7 percent per year. After 30 years, this battery will retain nearly 80 percent of its original capacity.
Conclusion
As usual, the answer to the engineering question is “it depends.” In this case, that question is, “what power source should I use for my wireless IoT?” Don’t assume that a rechargeable battery is the right or only answer, although it certainly may be. Determining the optimum answer requires weighing relative project priorities, risks, and other factors before making the decision.
Leave a Reply