A few back-of-the-envelope estimates show why it pays to maximize power supply efficiency.
Chris Harman • Puls l.p.
Engineers are becoming more sensitive to efficiency when selecting a power supply. Energy flows through the supply, and something less than 100% of that energy can be used because of inefficiencies of power supply components. The difference between usable energy and wasted energy is dissipated as heat. Heat is the enemy because it degrades the components in the power supply and other components in the electrical enclosure.
Suppose we have two power supplies, one 92% efficient, the other 96%. Both sound relatively efficient. Using these figures, we might think that the difference is only 4% (96% – 92% = 4%). But if we have a 100-W power supply, the 92% efficient power supply loses 8 W and the 96% efficient power supply loses 4 W. That is 50% less heat loss from the 96% efficient power supply.
Let’s look at a real-world example using two 480-W power supplies. The PULS CP20.241 has an efficiency rating of 95.6%. A competitive unit recently released has an efficiency rating of 93.1%. The apparent difference is 2.5%. At first glance, not a big deal. But as with the previous hypothetical example, the percentages hide a significant difference in energy use. A 95.6% efficient supply loses 21 W mainly to heat, while a 93.1% efficient supply loses 33 W, or about 57% more.
A simple method to determine the true difference of heat loss when comparing power supplies is to use the heat loss formula:
Heat is the number one enemy for power supplies because they normally use electrolytic capacitors. Electrolytics have a reputation for exhibiting a short service life when heat is a factor. The most common reason for reduced electrolytic capacitor lifespan is the evaporation or leakage of the liquid electrolyte. Environmental and electrical factors also play a role. Typical environmental factors that can shorten capacitor life include humidity, high temperature, mechanical vibrations, and humidity. Electrical parameters such as applied voltage, charge-discharge duty cycle, and ripple current can also lead to premature failure.
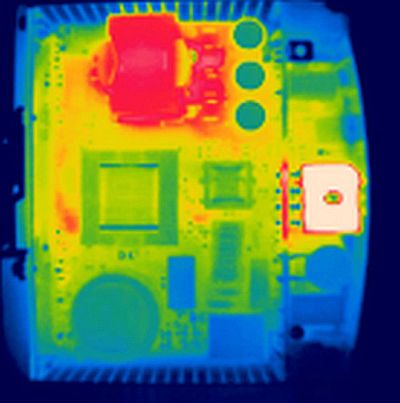
Datasheets define electrolytic capacitor service life under a nominal voltage, nominal current, and upper temperature limit . The temperature, ripple current, and apple voltage can accelerate aging. High temperature speeds the aging of electrolytic capacitors because it boosts the chemical reaction rate. A rise in temperature leads to the gradual evaporation of the electrolyte through the seal.
The life expectancy of an electrolytic capacitor is influenced by the applied voltage as well as the reverse voltage across the cap. Application of excessive voltage across the electrolytic capacitor boosts leakage current. The leakage current is responsible for internal gas generation and self-heating in the capacitor, which ultimately damages the capacitor’s internal structure. Reverse voltage above a few volts causes internal heating and pressure. If an electrolytic capacitor sees high reverse voltage, it may fail from the opening of the safety vent.
Ripple current through an electrolytic capacitor produces more internal heat. Discharge currents are catastrophic to electrolytic capacitor lifespans. The discharge current increases the internal heating and pressure, which reflects as the capacitance value drop during initial stages. With time, the charge-discharge duty cycle may lead to the destruction of the electrolytic capacitor by opening the safety vent to release gases.
The general rule of thumb, as published by capacitor manufacturers, is that every 10°C increase in temperature results in a 50% decrease in life for the capacitor. Since capacitors are so sensitive to heat, a good design will also thermally separate the capacitors from heat producing components like transformers and bridge rectifiers.
In addition to the drawbacks of electrolytic capacitors, often there are far more sensitive electronic components inside an enclosure which can be degraded by heat. In a nutshell, heat can radically reduce the reliability and lifetime of the power supply and other components in the enclosure. In many cases, it can force the use of a larger enclosure, the use of a cooling, or a derating of equipment to compensate for high heat losses.
Thus a power supply with the highest efficiency and good thermal design can mean the difference between a reliable control system and a system where problems ultimately will surface.
Design engineers must also consider the amount of energy necessary to operate the load. Referring to the example of the two 480-W power supplies, we can review them from an energy standpoint. The power supply which was rated 93.1% efficient and had 33 W of lost energy would, from a simplistic calculation, lose 1.65 kW over a 50-hr work week. The 95.6% efficient CP20 supply would have losses of only 1.05 kW. Using an average cost of 13¢/kWh. Thus the less efficient supply would waste approximately $11.16 annually vs. $7.10 annually for the CP20. Multiply this by the number of power supplies in use and the savings can be quite significant over the life of a control system.
Leave a Reply