by Sanjeev Manadhar, Texas Instruments
Hybrid electric vehicles (HEVs) and electric vehicles (EVs) are popular because they have low (to zero) emissions and fewer maintenance requirements while offering better efficiency and drive performance. New HEV/EV companies are emerging, while existing automakers are investing more in HEV/EV to compete for market share.
The heart of the HEV/EV powertrain lies in the system that takes the power from the grid, stores it in the battery (while stationary), and takes the energy from the battery to turn the motor and move the vehicle. This system primarily comprises four subsystems: the onboard charger (OBC), battery management system (BMS), DC-to-DC converter (DC/DC), and inverter and motor control (IMC), as shown in Figure 1. The flexibility and cost-benefit of amplifiers are often overlooked in the BMS of HEVs/EVs. Therefore, this article will focus on the BMS and how a designer may use amplifiers in the system.
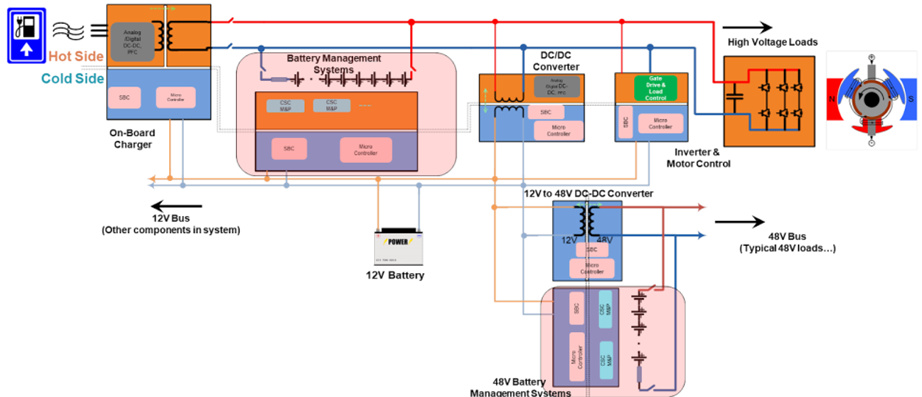
What does a BMS do?
The BMS maintains and monitors the battery, which includes charging and discharging it efficiently and safely. The BMS balances voltages and charges at each individual cell relative to each other, monitors battery health, keeps the battery at a safe operating temperature, and ensures longer battery life. The BMS should protect against conditions such as overdischarging the battery repeatedly, which will shorten battery life, or overcharging, which can damage the battery and cause a fire or explosion. The battery in an HEV/EV is a combination of many lithium-ion cells both in series and in parallel to meet the voltage and energy required. When fully charged, a single lithium-ion cell is 4.2 V and when discharged is close to 2.8 V. A fully charged battery in an HEV/EV can range from 200 V to 800 V. Figure 2 is a typical BMS block diagram.

Let’s review the primary functions of a BMS.
Battery current sensing
It is crucial to monitor the current going to the battery pack and the current leaving it. The magnitude of this current tends to be in the high hundreds of amperes in the main lithium-ion battery. A Hall-based sensor, induction-based sensor or isolated amplifier across a shunt resistor is typically used for current sensing across the cold side (low voltage) to the hot side (high voltage) of the battery. These isolated current sensing solutions could have analog differential output signals. The purpose of isolated current sensing is to keep the hot and cold sides separate and yet feed analog information about sensed current to an analog-to-digital converter (ADC) in the main microcontroller, powered by a low-voltage supply. This current sensing does not usually need to be very accurate. An op amp converts a differential signal to a single-ended signal (referenced to ground), increases the dynamic range, and drives the ADC. It is common to use a current shunt monitor for precise hot-side current sensing in BMS.
Figure 3 shows the circuit with an isolated amplifier and op amp at different voltage domains for current sensing with the DC transfer function. The voltage developed across the shunt resistor, VSHUNT, is amplified by an isolated amplifier as the differential output signal, VDIFF, at its isolated output. An op amp converts the differential signal, VDIFF, to a single-ended signal, OUT, and improves the dynamic range by applying a gain of 2 V/V to the signal. The isolated amplifier offset determines the initial current sensing accuracy. The common-mode rejection ratio of the difference amplifier is dominated by resistor tolerance.
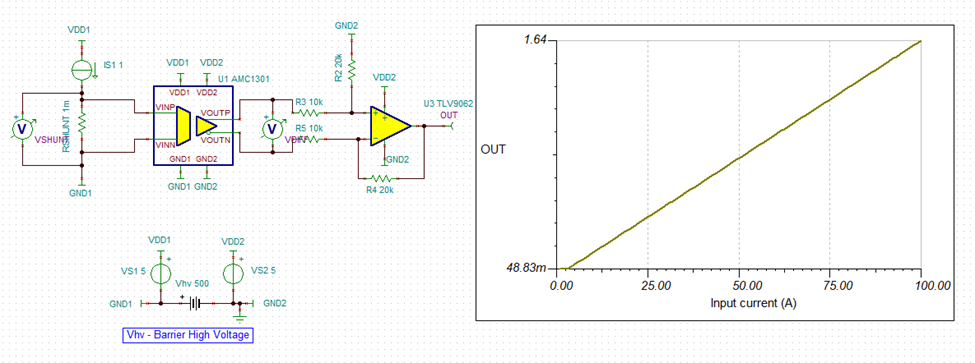
A DC-to-DC converter generates a separate 48-V battery subsystem from the main high-voltage battery in HEVs/EVs. This 48-V battery subsystem powers the air conditioning, heating, braking system, and power steering, and offers better efficiency than a conventional 12-V rail from a lead-acid battery. The 48-V subsystem does not have as high of a current load as the main battery but still requires current sensing, which is why it has its own local BMS. In 48-V BMS a non-isolated precision current shunt monitor is used for the main current sensing, and a bidirectional op-amp current-sensing circuit serves as redundant overcurrent protection. Figure 4 shows the op-amp circuit that conducts bidirectional current sensing.
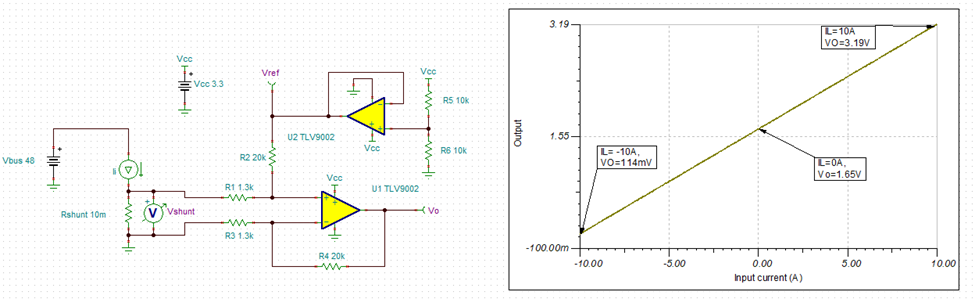
Battery voltage sensing
The voltage of the battery needs to be monitored just like the current. In isolated voltage sensing, a resistor divider divides the high voltage from the battery down to common-mode input range of an amplifier. An isolated amplifier senses the divided voltage, and an op amp used in a difference amplifier configuration converts a differential output signal from isolated amplifier to a single-ended output. If isolation is not needed, an op amp in a difference amplifier configuration can perform direct voltage sensing.
Figure 5 shows isolated voltage sensing with an isolated amplifier and an op amp. An isolated amplifier isolates the hot and cold sides and outputs a differential signal with a gain of 1. An op amp converts the differential signal to single-ended output and gains up for the ADC to meet the full dynamic range. This voltage is fed to an ADC in the MCU at the cold side.
An integrated power chip designed specifically for BMS tracks the voltage of each lithium-ion cell and balances the charge. Daisy-chaining these power chips can measure voltages across all of the lithium-ion cells at once, balance voltages across these cells and communicate this information to the MCU.

Isolation leakage current measurement
As I mentioned earlier, the high-voltage 200- to 800-V side is kept isolated from vehicle chassis ground and other lower-voltage domains (12 V and 48 V). Measuring the voltage of the battery and the leakage current through a test isolation break will also result in a measurement of the resistance or leakage between the high-voltage rail and low-voltage of chassis ground. The Automotive High-Voltage and Isolation Leakage Measurements Reference Design explains the test isolation break, which entails temporarily shorting the isolation barrier with a known resistive path, as shown in Figure 6.
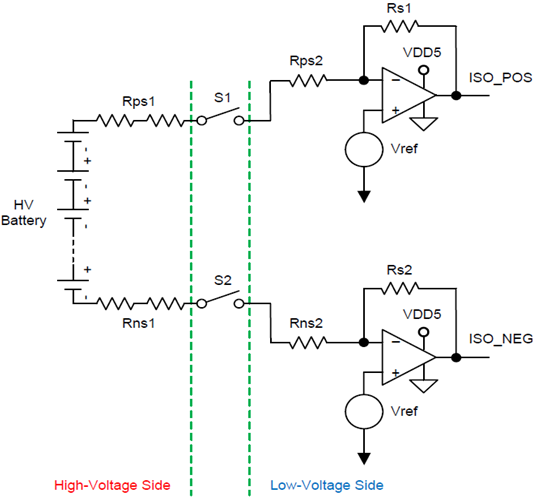
Figure 6: Isolation leakage current measurement circuit with an op amp
It is necessary to know the path of faulty breach leakage current from the positive or negative sides of the high-voltage battery. One isolation break occurs at a time, with relay S1 at the positive side or relay S2 at the negative side. Comparing this known isolation resistance to the measured resistance will determine the leakage through the isolation barrier.
For example, the ISO_POS voltage will be equal to Vref when S1 is closed and if there is no leakage at the negative side. If there is leakage current (an isolation breach) at the negative side, the ISO_POS voltage will not be equal to Vref. The closed-loop gain is different because of leakage current flowing through Rps1, Rps2, and Rs1, the positive side and negative side of the battery to the low-voltage side ground. An op amp with a low input bias current is suitable for this application as the impedance connected to an inverting input can be very high (in the megaohm range).
Temperature monitoring
An HEV/EV requires high voltages and high currents, which could lead to high power dissipation, and fast temperature rises. It is absolutely necessary to monitor the temperature of the battery and system around it to prevent the dissipation of excessive power. If a faulty condition leads to high power dissipation, the battery control unit will disconnect the battery to prevent catastrophic events like fire and explosion.
One cost-effective solution for temperature sensing is to use an op amp to buffer the signal from a negative temperature coefficient (NTC) thermistor in series with a resistor. Since the BMS and battery occupy a large area, the temperature may not be uniform throughout this system. This nonuniformity in temperature necessitates multiple temperature sensing units placed throughout the BMS. Multiplexing the signals from these units to a single ADC or MCU pin will require signal conditioning. The signals also need to be buffered and amplified to meet the ADC’s full dynamic range.
Figure 7 illustrates an op amp used in buffer amplifier or noninverting amplifier configuration. A low-cost, high-voltage op amp with reasonable offset and offset drift is suitable for this application.
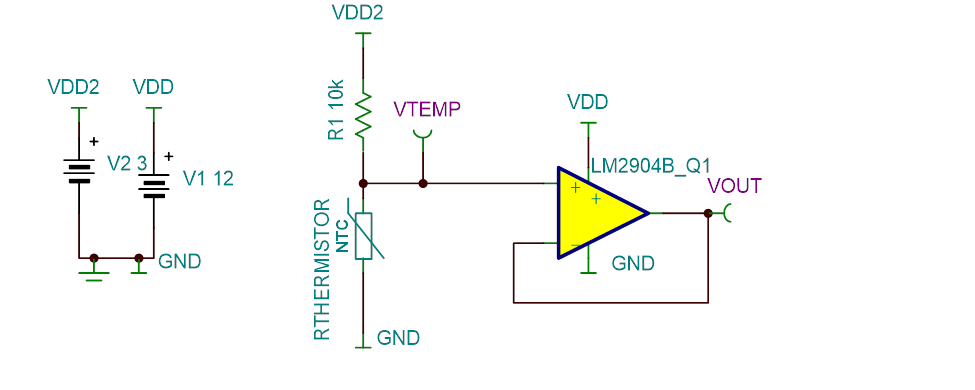
Interlock monitoring
Interlock is a voltage and current loop system that flows through a series of subsystems in an HEV/EV system, as shown in Figure 8. Interlock starts from the BMS and goes through the inverter, the DC/DC converter, the OBC and back to the BMS to monitor any tampering, opening of the high-voltage system, or opening of the service hatch. The Automotive High-Voltage Interlock Reference Design explains how interlock system disconnects the high-voltage line to prevent injury.
The interlock loop mostly involves sensing current that is transmitted in pulse that does not require high accuracy measurement. The compact solution requirement could lead to an instrumentation amplifier-based solution. The most economical solution is to use a current-sensing circuit with an op amp and discrete resistors in a difference amplifier configuration. The interlock loop is not a high-current loop; thus, you can use a high-value shunt resistor without the risk of high power dissipation. The safety and diagnostic functions require redundancy to cover situations when the primary system fails. To detect all possible faults, there may be more cases that require secondary voltage and current sensing, and where the low-cost solution becomes more viable.
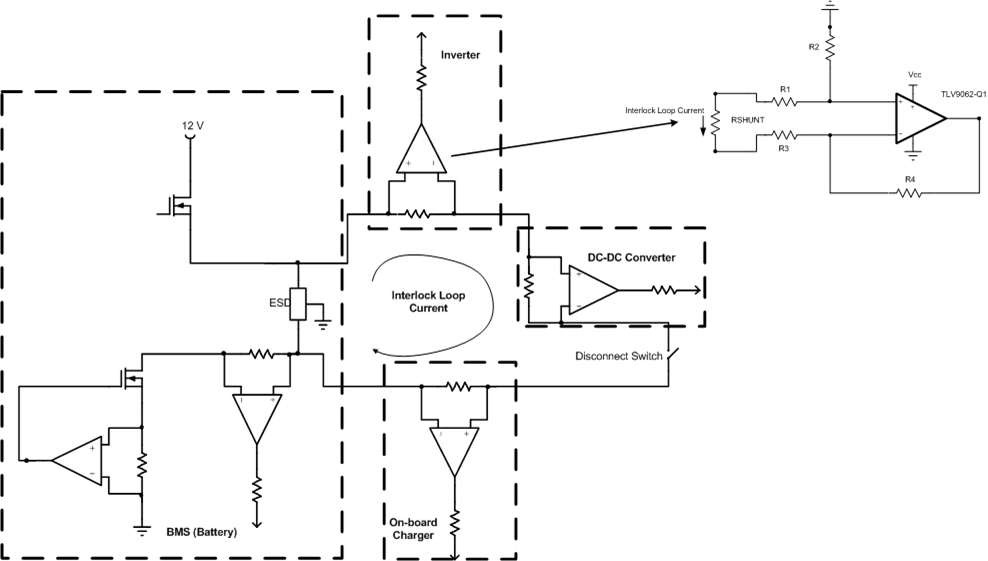
Conclusion
These are all standard functions in a BMS using an amplifier, but there could be more functions for which you could use op amps, depending on system design. An op-amp-based solution becomes more practical when the problem is new or unusual, and an integrated solution does not exist. The systems in EVs/HEVs are evolving and it is becoming common to find situations where op amps provide a quick, accurate, and flexible solution.
References
Leave a Reply