Modern hardware applications trend towards compact designs that are power efficient. Passive devices don’t get as much attention as a microcontroller’s many sleep and shutdown states. However, every drop of available efficiency adds up and can make a difference. It’s possible to improve power efficiency with the right inductor.
Power inductors are a necessary component in many designs, including DC-DC converters, point-of-load (POL) power modules, field-programmable gate arrays (FPGAs), and battery-powered regulators, to name a few. Reducing power losses depends greatly upon an inductor’s core material. The size of the physical package is often critical, too. Designing becomes even more difficult as the size of a device decreases and current increases.

Inductors store energy by changing electrical energy into a magnetic field that’s measured in Henries (H). An inductor’s coil generates a magnetic field when current runs through the windings (Figure 1). An inductor’s ability to store energy is influenced by many parameters. The larger the number of wire-turns in the coil, the greater the inductance value (i.e., more Henries). The greater the inductance value, the greater the amount of energy that can be stored. Inserting a magnetic material inside the core of the coil increases the strength of the inductor’s magnetic field.

Inductance can also be increased by creating a core with a larger cross-section, using highly permeable core material, and to some extent, by increasing the length of the core. Permeability is a magnetic characteristic. Core materials with a higher permeability generate a higher density of magnetic flux, which allows more energy to be stored. Therefore, the inductance value (H) is proportional to the permeability of the inductor’s core material.
If the core material is highly permeable, one can reduce the size and weight of the inductor without reducing the inductance value. Just increasing the core’s permeability can preserve the inductor’s performance while lowering the cross-section of the inductor’s core so the overall package is smaller and lighter. Increasing a core’s permeability allows the same performance with fewer turns (n) of the coil, enabling a smaller inductor with a smaller amount of turns and thinner wire, too (Figure 2).
Permeability is a critical factor in an inductor’s core material. There are many different types of inductor cores besides air, laminated cores, including iron, ferrite, iron powder, metal composites, and silicon steel, or “electrical steel.” These core materials respond differently as an inductor operates across different power levels, frequencies, and temperatures. Iron cores have been in use for a long time. Ferrite cores are a ceramic material that’s mixed with iron oxide and a few other metals to form a core with high permeability and good temperature properties.
Iron powder cores are made of iron particles mixed with other materials. Metal powder or metal composite cores are made of a material that includes magnetic metallic particles, binders, coatings that insulate particles, and even small homogeneously distributed air bubbles throughout the core (Figure 3).
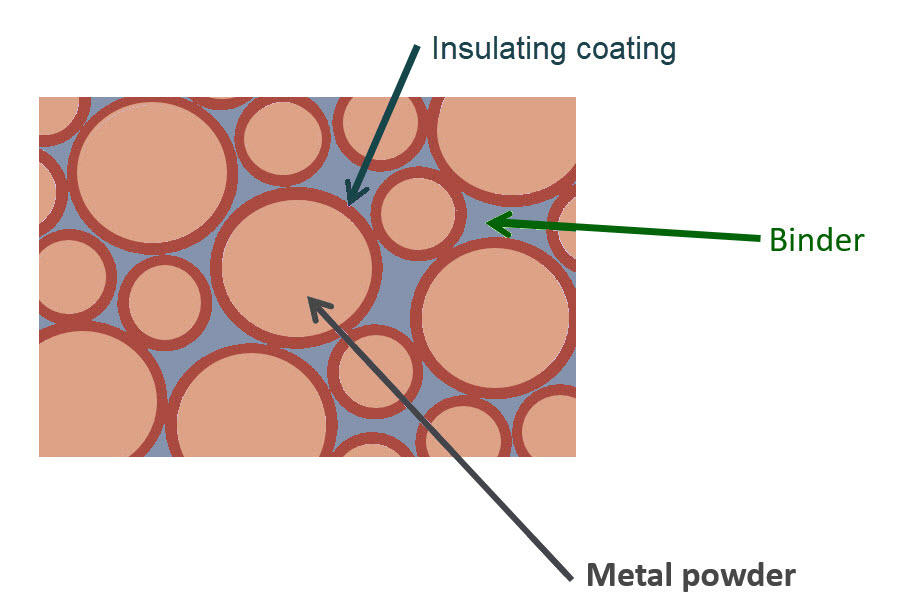
Metallic composite materials can be shaped or molded into geometries amenable to a power inductor’s advantage. The metallic particles are mixed with a binding material, molded, and then cured. Since the metallic composite material is moldable, it can serve double duty as a shield if the core is formed around the coil, on the outside of the coil. Although inductor cores are typically located on the inside of a coil, a core like this can serve as a shield to reduce escaping magnetic flux. Molded inductors with cores that act as shields can be located adjacent to sensitive circuits, thus enabling higher density designs. Composite metal core materials can have high permeability, allowing a smaller sized inductor without compromising performance.
Leave a Reply