Traction motors are optimized for locomotives, EVs, elevators, and other situations where high torque at start-up and low speed is needed.
The final part of this article examines additional traction-motor issues.
Q: What about physical size and associated issues in traction-motor applications?
A: Inner-city urban light-rail vehicle (LRV) floors are typically low since the stops for these trams have low or no platforms. The low floor reduces the available space for the traction motor, which is mounted close to the ground (down to 60 mm), and the motor operates in a polluted environment involving dust, sand, or debris. Further, these trams have frequent start/stop cycling, and the motors heat up during acceleration and deceleration.
Q: How does this affect the cooling situation?
A: As there are few or no higher-speed runs from stop to stop, obtaining adequate air cooling is a problem and liquid cooling may be needed. Due to the polluted operating environment, many urban LRVs must use a closed cooling arrangement to protect the motor’s sensitive components (Figure 1). This scheme, however, reduces cooling performance.
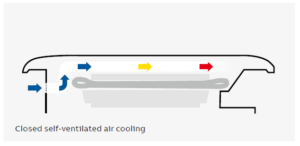
Q: How does the situation differ for suburban rail vehicles?
A: In contrast, suburban cars typically are high-floor LRVs as they are accessible via platforms at stops. Additionally, since the distance between stops is longer, the vehicles can run at higher average speeds, making self‑ventilated cooling concepts more favorable than with inner‑city trams. These trams usually operate on separate tracks which are away from cars and buses, so there is less pollution. As a result, an open-cooling approach can be used, which provides for more-effective cooling and heat dissipation (Figure 2).
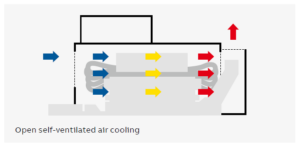
Q: None of the motors discussed thus far use permanent magnets, yet PM motors are increasingly used in many applications. What’s the PM situation for traction motors?
A: The PM motor is a 3-phase AC synchronous motor, but with the usual “squirrel cage” construction replaced by magnets fixed in the motor. The motor requires a complex control system, but it can be up to 25% smaller than a conventional 3-phase motor for the same power rating. The design also gives lower operating temperatures so cooling requirements are simplified.
Some traction motors now use PM motors, including 25 AGV high-speed train sets and LRV trams in France and Prague as well as Tesla vehicles. The reduced size is particularly attractive in low-floor LRVs where hub motors can be combined in a compact bogie.
Q: All this locomotive and LRV discussion is interesting, but what about traction motors for mass-market electric vehicles?
A: Each EV vendor has technical, market, and cost reasons for choosing a specific motor arrangement. For example, Tesla uses a combination of motor types including PM types as space is very limited (Figure 3). To compare kilowatts to horsepower (cars are specified in kW, while railway motors are often specified in horsepower), note that one horsepower is around 750 watts.

Q: Are there standard, off-the-shelf power sources and controllers for traction motors?
A: Yes and no. Most are custom designed for the application performance and specifics, as the unit volumes are high enough to absorb the engineering cost while achieving optimal performance across multiple parameters. Even a percentage point or two in efficiency improvement is critical in EVs due to range objectives and cooling, while for LRVs and catenary-powered locomotives, it affects cooling challenges and power costs rather than range.
Q: So, are there standard power units and controller units for traction motors?
A: There are some. For example, Curtiss-Wright recently introduced 100-800 VDC input/420-kW (at 700 VDC) inverters for single-motor (CWTI-S420) or dual-motor (CWTI-D420) applications in electric busses, hybrid vehicles, and diesel-electric off-road vehicles (Figure 4). For flexibility, both models can feed power to a wide range of motor technologies, from AC induction and permanent-magnet synchronous (PMS) to interior permanent-magnet (IPM) types.
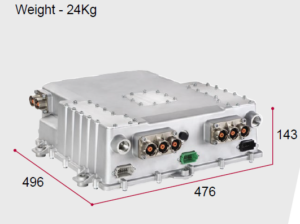
The advanced motor-control software within its new traction inverters runs adaptive tuning to get higher levels of efficiency between the inverter and motor. The result is up to 2% better efficiency in the drive system (motor plus inverter), according to Curtiss-Wright.
These ruggedized traction inverters use vehicle-grade components certified to AEC Q-100, 101, and 200 standards and adhere to ISO 26262, an international functional-safety standard for the development of electrical and electronic systems in road vehicles. It defines guidelines to minimize the risk of accidents and ensure that automotive components perform their intended functions correctly and at the right time.
The CWTI units offer full fault protection and a high level of self-protection, as current and temperature are measured directly and accurately on the IGBTs. These measurements help get higher power from the motor, while current measurements offer superior short-circuit protection to the system.
Conclusion
Traction motors are an important class of electric motors. They are optimized for high torque at start-up and low speed among other attributes and can be implemented via different motor arrangements. They power small movers such as forklift trucks, and large systems such as all-electric and diesel-electric locomotives. With the increased development of consumer electric vehicles, they are also seeing many advances in performance and packaging. Modern electronics have made the older brushed DC motor less attractive and supplanted it in many cases with various AC-based motor types using IGBTs and MOSFETs for power switching under processor control.
Related content
The brushed DC motor: Still a very viable option, Part 1: Operation
The brushed DC motor: Still a very viable option, Part 2: Applications
Electric locomotives and catenary power systems – Part 1: basic functions
Electric locomotives and catenary power systems – Part 2: power needs
Electric locomotives and catenary power systems – Part 3: power delivery
Electric locomotives and catenary power systems – Part 4: maintenance and corona
Basics of motion-control profiles, Part 1: Context
Basics of motion-control profiles, Part 2: Ramp profiles
Basics of motion-control profiles, Part 3: Implementations
Motor fundamentals and DC motors
SiC gate driver benefits traction inverters for EVs
Discrete 750-V IGBTs optimized for automotive traction inverters
Full SiC power module optimized for electric/hybrid traction motorsports apps
IGBT power modules optimized for EV traction inverters
Magnetic gear tooth sensor IC optimized for traction motor apps
Wide-input-range, high power density dc-dc converters optimized for railway traction, rolling stock apps
External References
Medical Design Briefs, “Every Drop Counts: Designing Motors to Optimize Home and Ambulatory Infusion Pumps”
Electrical Desk, “Different Types Of Traction Motors”
Everything PE, “What is an Electric Vehicle Traction Motor?”
Wikipedia, “Traction Motor”
Springer, “Vehicle Traction Motors”
The Railway Technical Website, “Electric Traction Control”
ABB, “ABB traction motors — Light rail vehicle (LRV)”
ABB, “Let’s go electric now! Advanced e-mobility drivelines”
Monolithic Power Systems, AN047, “Brushless DC Motor Fundamentals”
Curtis-Wright, “CWTI-D420 New Generation Dual Traction Inverter Sales Brochure”
Curtiss-Wright, “Traction Inverters Data Sheet”
Texas Instruments, “Technical White Paper Design Priorities in EV Traction Inverter With Optimum Performance”
Texas Instruments, “Design Priorities in EV Traction Inverter with Optimum Performance”
Texas Instruments, “Enhance the Design of HEV/EV Traction Inverter Systems Using Isolated IGBT and SiC Gate Drivers”
Leave a Reply