by Patrik Kalbermatten, KEMET
Protecting sensitive electronic equipment against transient voltages in the form of surges that may be either circuit emanating from relays or motors, or significant ESD events such as lightning strikes, is a vital part of equipment design.
Several technologies exist to protect sensitive electronic circuitry from voltage surges, including gas discharge tubes, transient voltage suppression diodes, and metal oxide varistors. While each of these is an effective solution, some are naturally more suited to modern applications where space is at a premium and cost is a key consideration.
What are ESD events, and why are they a challenge?
Electrostatic discharge (ESD) is the sudden flow of electrical energy between two charged objects. This can be caused by physical contact or an electrical short, or as a result of a dielectric breakdown. The most spectacular type of ESD is lightning during a storm which is categorized as a large-scale ESD event. However, sparks can be produced by smaller events, which are a serious threat in areas containing gas or fuel vapor. ESD can also be very harmful to electronic components, which can suffer permanent damage or even failure as a result.
ESD events almost always result from the build-up of static electricity, and this is most often caused by a phenomenon known as triboelectric charging, where two dissimilar materials come into frictional contact. Modern materials such as cotton, wool, polyester, and other clothing materials are particularly susceptible to triboelectric charging, making humans a key source of ESD events and providing a widespread challenge to the electronics industry, as protection against ESD events is required in all products.
Comparison of TVS diodes and varistors
While several techniques exist for the suppression of the fast-moving spikes caused by ESD discharge including gas discharge tubes (GDTs), two of the most commonly used are transient voltage suppression (TVS) diodes and metal oxide varistors (MOVs). While they both protect a circuit, there are some significant differences.
A TVS diode is a semiconductor-based device that is designed to divert or shunt voltage spikes from a circuit to provide protection. Their main advantages are that they typically have a fast response time (often less than 1ns) and also a low clamping voltage. However, their energy density cannot match that of equivalent-sized varistors, and if they were to try and dissipate the same amount of energy as is possible with a varistor, they would be damaged. Overall, their power capability is relatively limited, and when they fail, it is normally as a short circuit causing issues for the circuit they are intended to protect.
Varistors are essentially voltage-dependent resistors, meaning that their resistance changes in response to the voltage applied to them. While their response time is typically microseconds, they offer higher surge capabilities and a wider range of breakdown voltages than a TVS. One of the most striking differences between the two types of device is the relative size for a given energy absorption – the difference is significant as shown in figure 1 where a similarly sized varistor is rated for ten times the current, or a similarly rated device is at least ten times smaller than the comparable TVS.
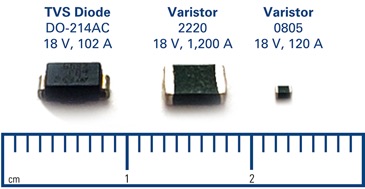
As modern portable devices such as smartphones and tablets are particularly at risk from ESD events, this size difference (often referred to as a far higher energy density capability) is significant as it allows effective ESD protection to be included in the limited footprint available. The fact that varistors are generally lower cost than TVS devices is another factor that makes them particularly suitable and interesting for designers for these types of applications.
Design and construction of a varistor / MOV
As mentioned, varistors are voltage-dependent resistors. However, their construction is very similar to a capacitor, and their function is similar to a diode. In the simplest terms, they consist of two metal plates with a resistance material sandwiched between. The resistance material is primarily (around 90%) zinc oxide (ZnO) with some other filler materials to form junctions between the ZnO grains that have been pressed into a ceramic-like material.
The use of ZnO means that the energy absorption in a varistor takes place across almost the entire volume of the device, whereas for a TVS, only the small PN junction area is available for suppression. This is one of the main reasons why a MOV typically has far superior energy density performance when compared to a TVS.
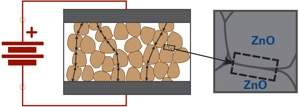
This metal oxide (ZnO) makes MOVs very effective in absorbing voltage transients and provides the devices with the ability to handle high levels of energy in a small size. MOVs start conduction at a specific voltage and stop conduction when the applied voltage falls below a threshold level.
While varistors are available in leaded packages with an epoxy coating where they look very similar to disc ceramic capacitors, they are also available in surface mount packaging allowing for use with modern production processes.
Selection considerations
To select the correct varistor for a given application and, therefore, ensure that the circuit is adequately protected, there are a number of factors for designers to consider. The challenge is often compounded as to make a completely accurate selection it is necessary to know the source impedance and pulse power of any possible transients and, as naturally-occurring phenomena, this is often not possible.
From an electrical perspective, the designer will generally consider the working voltage of the system requiring protection as well as the maximum transient voltage that the system can withstand.
As far as the designer can, determining the possible overvoltages and their characteristics in terms of shape, amplitude, and duration is also useful information to have – as is knowing whether surges are likely to repeat.
Alongside this, the designer will consider the AC and DC voltage ratings of the component, operating temperature range, capacitance value, and physical size. Many varistors also carry relevant approvals for particular applications, including AEC-Q200 for modern automotive applications.
Summary
Clearly, varistors are a compelling proposition for modern electronic devices due to their ability to handle relatively large energy discharges in a small package size, with an acceptable cost.
KEMET’s varistors offer ratings to 385 V, and the ability to handle surge currents as high as 1,200 A. The devices are available in packages as small as 0603, yet can operate in harsh environments with temperatures as high as +150°C. Many of the devices carry AEC-Q200 qualification for the growing number and diversity of automotive applications.
One additional feature of KEMET varistors is that some are available as dual-function devices with X7R capacitors built into the same package, thereby providing suppression and snubbing in a single package to reduce component count and enhance circuit reliability.
Leave a Reply