When the task calls for a aerial system that can hover in place, the often-chosen approach is to employ a tethered drone. A tethered drone, generally a multirotor, gets its power and communications signals via a flexible wire or cable. Where battery powered multirotor drones can exhaust their batteries in 20 minutes or so, tethered drones receive their power through the tether from a base station. This enables them to stay aloft for hours or days.
One limiting factor of the scheme is the weight of the tether. Every ounce of tether weight is one less ounce available for the drone payload. So drone tethers may be made of aramid or other lightweight synthetic materials to provide strength, with copper or plated copper for power conduction and optical fiber for data and communications.

For similar reasons, designers endeavor to keep the tether power wires light weight. So the usual approach is to use a high voltage/low current supply at the base station to minimize the size of the tether conductors, then down-convert the voltage on the UAV.
This is the approach used by DPI UAV Systems in Essington, Pa. on its Unmanned Multirotor Aerial Relay (UMAR). UMAR is a tethered drone that lifts 15-lb payloads, such as communication antennas, up to 500+ ft in the air. By levitating an antenna, the UMAR system can extend boat/ship radio line-of-site from eight miles to 30 miles, thereby boosting communication range.
UMAR consumes 8 to 10 kW, all of which is supplied via the tether. DPI down-converts 800-V power coming up through the tether into 50 V via Vicor Ultra High-Voltage (UHV) BCM VIA modules. Eight BCMs power the UMAR’s eight independent rotors, with the ability to share power among the rotors in parallel for redundancy. An additional onboard UHV BCM powers the avionics, autopilot and payload.
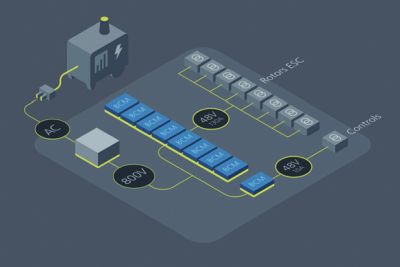
The UHV BCM4414 modules are fixed-ratio dc-dc converters providing high-efficiency conversion (98%) — higher efficiency than would be available from regulated converters. Measuring just 4.35×1.40×0.37 in (110.55×35.54×9.40 mm), these modules obey PM Bus commands and provide up to 776 W/in3 power density while incorporating integrated EMI filtering.
The low-profile, flat-sided power modules sit in two waterproof–to prevent moisture ingress from saltwater and rain–aluminum enclosures and mount to the host PCBs in an architecture that allows two-sided cooling. A system of heat pipes and heat sinks provide passive cooling when the drone is on the host vessel. When airborne, the spinning rotors provide additional active cooling.
A low-voltage-side-referenced PM Bus-compatible telemetry and control interface provides access to fault monitoring and other telemetry functions. This PM Bus capability allows UMAR operators to monitor system temperatures, voltage and currents in real time, information which is particularly valuable in hot climates.
Integrated EMI filtering built into the Vicor UHV BCMs helps minimize electrical noise that might otherwise garble RF communications between the drone and host or support vessels. Minimization of conducted EMI on the tether is especially important when the drone operates near radio equipment. UHV BCMs provide a clean EMI signature with few harmonics. A small companion filter reference design outside the VIA package cuts conducted EMI levels to well below typical requirements.
“Using Vicor power modules, we have been able to lower the weight of all components onboard the drone to increase altitude and airspeed while carrying the required mission payload,” said Joe Pawelczyk, Vice President of Operations at DPI. “Nobody else really has the power density of Vicor, so we can achieve top levels of maneuverability, performance and hover control with their components. This enables DPI tethered drones to lift more, fly higher, and fly faster.“

UMAR is designed to maintain stationary positioning in severe maritime storm conditions. The task is often complicated by turbulent waters that toss around the host vessel. So the drone requires the power capacity and agility to accelerate rotor speeds for lift and yaw in short or prolonged bursts to maintain altitude – with instantaneous responsiveness.
Tested extensively in real-world operating conditions, DPI tethered drones are currently being qualified for use by the U.S. Navy in marine and maritime environments for intelligence, surveillance, reconnaissance (ISR), communications and video applications. The system has been designed to withstand harsh temperatures from zero to 120°F. These drones can provide 400+ hours of nonstop up time and operations.
In addition to its current trial deployments with the U.S. Navy, DPI technology is being evaluated by government agencies, contractors and other entities. It has shown significant promise for additional applications like first-response disaster relief and large-area monitoring (public events, stadium security, etc.). Anywhere a hover-in-place communications and surveillance presence might be needed, DPI multirotor drones could be readily deployed.
thank you for the article