The high performance of many autonomous automotive features will likely depend on the use of super-fast GaN semiconductors.
Alex Lidow, Efficient Power Conversion (EPC)
WITH the rise of autonomous cars and electric propulsion as driving forces in automotive applications, a huge new market for power devices based on gallium nitride grown on a silicon substrate (GaN-on-Si) is emerging. IHS Markit estimates that 12 million cars will be autonomous by 2035. According to Bloomberg New Energy Finance, Marklines, 32 million cars will have electric propulsion. Both trends are putting performance demands on power semiconductors. These demands are coming at a time when silicon is reaching its performance limits, thus further opening opportunities for GaN technology devices.
Over the past eight years GaN power devices have been in mass production. And there have emerged several large automotive applications where GaN has significant advantages over the aging silicon MOSFET: LiDAR (Light Detection and Ranging), radar, 48-to-12-V dc-dc conversion, ultra-high-quality infotainment, high-intensity headlamps, and on-board wireless power charging.
One of the first automotive applications for GaN transistors and ICs was in LiDAR. Use of this object detection and distance measuring technology was prompted by the need to gain critical information as quickly as possible about a self-driving car’s surroundings. Velodyne was the first LiDAR company to recognize the contribution that the superior switching speed of GaN can make to an autonomous vehicle’s LiDAR system.
By triggering high-current laser pulses that are extremely narrow, it is possible to accurately measure the time-of-flight for emitted photons, and there will be enough photons reflected to see objects at long distances. The more frequently a LiDAR system can fire its laser, the more information obtained about the surroundings. The combination of high current, narrow and frequent pulses makes it possible to rapidly resolve objects with an accuracy of a few millimeters at distances of a few hundred meters.

Velodyne implements LiDAR using a spinning disk carrying several solid-state lasers stacked parallel to the axis of rotation. The resulting laser beams create a fast and accurate digital point cloud identifying the surroundings of a self-driving car.
The laser optical pulse has two main parameters: pulse width and energy. These two factors have a large effect on the distance resolution and the range, respectively. The pulse width of the transmitted optical signal has a great influence on the LiDAR system. Given that the light pulse must travel to the target, be reflected and travel back, the time td between pulse transmission and reception for a target at distance d,
td = 2d/c
where c is the speed of light in air. Various signal processing techniques can improve the resolution for a given pulse width. But it is clear a shorter pulse gives better inherent precision, and pulses on the order of a few nanoseconds are desirable for human-scale resolution.
Pulse energy determines the range of the LiDAR. As demand for better resolution drives designs towards narrower pulses, the pulsed current must rise to maintain sufficient pulse energy.
GaN FET high-speed devices can create high-current pulses with extremely short pulse widths. This is one reason Velodyne chose eGaN FETs from Efficient Power Conversion as the triggering devices for firing the laser.
LiDAR is just one of the technologies developed for autonomous vehicles. The large amount of data generated by the array of LiDAR sensors used in vehicle navigation and control, combined with data provided by radar, cameras and other information-gathering devices on the car, has fostered a new market for high-performance graphic processors. These processors integrate multiple sensor inputs, digest their meaning, and decide what commands to send to the self-driving actuators.
Fast processing is a key attribute. So companies such as NVIDIA Corp. and Intel’s Mobileye have developed ultra-fast multicore processors. These processors can gather, integrate and make sense of all the inputs from multiple radar, LiDAR, camera, and ultrasonic sensors quickly enough to safely navigate our roads and highways.
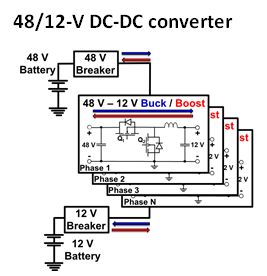
High-performance processors for autonomous vehicle navigation are extremely power hungry. The need for power places a heavy burden on traditional automotive 12-V electrical distribution buses. Consequently, automakers increasingly turn to 48-V distribution buses to provide enough power. Use of a 48-V bus reduces current levels and wire sizes by a factor of four.
The advantages of 48 V are even more evident when considering all the new power-hungry electronically-driven functions and features on the latest cars. Among them are electric start-stop, electric steering, electric suspension, electric turbo-supercharging, and variable-speed air conditioning. These new functions and features generally need 48 V – 12 V dc-dc converters. GaN power transistors help these power supplies operate efficiently. They take power at 48 V and convert it to 12 V to run legacy systems and battery packs. IHS Automotive estimates that 11 million cars will have 48-V systems in 2025.

GaN FETs and ICs have the highest power density and are the most efficient way to reduce 48 V to 12 V. GaN devices are many times smaller than equivalent silicon power MOSFETs and many times faster. The resulting electronics can have high efficiency while being smaller and less expensive. eGaN FETs from EPC are also competitive with silicon when it comes to volume pricing. And for the automotive market, GaN technology has promoted wide-spread adoption by passing AEC-Q101 qualification testing. In terms of reliability, eGaN technology has been mass produced for over eight years, accumulating billions of hours of successful field experience in automotive applications.
EPC and other GaN product suppliers, such as Transphorm and GaN Systems, have products undergoing AEC-Q101 qualification testing. Two of these products, EPC2202 and EPC2203, are EPC discrete transistors that have completed qualification tests. The devices are in wafer-level chip-scale packaging (WLCS) with 80 VDS ratings. They are harbingers of future eGaN discrete transistors and integrated for the harsh automotive environment.

The EPC2202 is an 80-V, 16-mΩ enhancement-mode FET with a pulsed current rating of 75 A in a 2.1×0.6-mm chip-scale package. The EPC2203 is an 80-V, 73-mΩ part with a pulsed current rating of 18 A in a 0.9-mm2 chip-scale package. These eGaN FETs are many times smaller and realize switching speeds 10 to 100 times faster than their silicon MOSFET counterparts. Both products are designed for a wide range of emerging automotive applications. In addition to LiDAR and dc-dc conversion, they also include high-intensity headlights and ultra-high-fidelity infotainment systems.
To complete AEC-Q101 testing, these eGaN FETs had to undergo rigorous environmental and bias-stress tests that include humidity with bias (H3TRB), high-temperature reverse bias (HTRB), high-temperature gate bias (HTGB), temperature cycling (TC), as well as several other tests. Of note is the fact that these wafer level chip-scale (WLCS) devices passed the same testing standards created for conventional packaged parts. Thus chip-scale packaging does not compromise on ruggedness or reliability. These parts are produced in facilities certified to the Automotive Quality Management System Standard IATF (for International Automotive Task Force) 16949.

Throughout 2018 additional 80-V parts will undergo certification, expanding the range of performance to higher currents. The stage is set, the future will see an expanding adoption of GaN devices for many traditional and emerging automotive applications.
Leave a Reply