Supercapacitors now come in a small, thin format that makes them candidates for uses characterized by cramped quarters.
Shinji Higuma, TDK Corp.
In the next several years, the internet of things (IoT) will include tens of billions of connected devices. Consumer, industrial, medical, and automotive applications will feature connected devices, but not all connected devices will be phones, machinery, healthcare equipment or vehicles. A large percentage of what’s connected to the IoT will be small, remote endpoints with relatively simple features. Many will have narrowly defined uses such as monitoring the temperature of food in a catering operation.
Despite the many different types of smart endpoints, their basic architecture is broadly similar. It includes a processing capability, a form of communication (typically wireless), and a source of power with associated power management.
Some IoT endpoints may not have access to reliable offline power. And adding offline rectification and regulation could be too expensive for many smart endpoints. A primary or secondary (rechargeable) cell might be an option. The CR2032 coin cell battery is a favorite and can deliver many years of service in a lot of applications.
Battery lifetime depends on the endpoint’s operating conditions. If the endpoint provides critical data, the manufacturer might add a supplementary power source that steps in if the main source is depleted.
Energy harvesting involves converting ambient energy from heat, vibration, solar and other sources into electricity. There are many microcontrollers (MCUs) and processing modules having power requirements low enough to operate just from harvested energy. But while it’s feasible to operate a smart endpoint from harvested energy, the means of storing the energy most efficiently remains an issue.
Electrolytic capacitors can store energy short-term with a relatively high power density. In applications requiring a short energy burst, such as driving an electromechanical actuator, a large capacitor is a good option. However, conventional capacitors are large and subject to aging. As a longer-term form of backup power, they are not an ideal technology.
Inside EDLC technology
An alternative growing in popularity is the Electric Double Layer Capacitor (EDLC). EDLCs are manufactured in various forms, including chip, coin cell and pouch. Cell type devices are also packaged in modules or stacked. The pouch-type EDLC is supplied in a soft, flexible foil-based pouch that can easily conform to irregular shapes. This makes the pouch-type EDLC suitable for thin and light circuit designs.
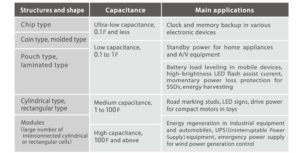
Like a capacitor, EDLCs store energy as charges (the charge carriers are ions in EDLCs) that adhere to an activated carbon electrode. Electrically, EDLCs behave like conventional secondary battery cells. But EDLCs can recharge in seconds rather than the minutes needed to recharge secondary cells which are based on chemical reactions. Thus EDLCs have a higher power density than that of batteries. Power density refers to the amount of time needed to charge and discharge energy. EDLCs have faster charge and discharge rates than batteries because the chemical reactions within batteries take longer to release electrons than the electrical discharge in EDLCs.
EDLC electrodes typically have a make-up that includes 70 to 95 wt% carbon-based material, binder, and other conductive additives (often carbon black) to enhance electrochemical properties. The structure of the activated carbon capacitance largely defines an EDLC, including its specific surface area, volume and pore diameter. The electric double layer capacitance is roughly proportional to the accessible surface area of the electrolyte ions, hence the use of activated carbons as electrode materials. The high capacitance of the activated carbon arises from the high specific surface area (>1,000 m2/g) provided by the presence of many micropores. But this structure also gives EDLCs a significant internal resistance. For applications that require a large current, it’s best to select an EDLC with the lowest possible internal resistance.

Manufacturers such as TDK can construct EDLCs with capacitances exceeding that possible with other types including aluminum electrolytic, film, ceramic and tantalum. However, most other capacitors feature a higher operating voltage. Consequently, EDLCs are candidates for power sources if the supply voltage is relatively low, as with smart endpoints which routinely operate at voltages of 3.3 V or less.
EDLCs can store energy for long periods, but they exhibit a leakage current. There are three main contributors to leakage current: charge redistribution, faradaic reactions, and ohmic leakage. Charge redistribution arises from the movement or loss of charged ions adsorbed on the electrode. Faradaic reactions are oxidation or reduction reactions on the electrode surface caused by overcharging or the presence of impurities. Ohmic leakage comes from internal ohmic leakage pathways between the positive and negative electrodes. The structure of an EDLC, in conjunction with its operating environment, will determine the magnitude of the leakage current.

Engineers should factor leakage current–even when the EDLC is fully charged–into power calculations. Energy harvesting applications may be able to compensate for leakage current losses if the average energy available exceeds the level of leakage current.
With its small size and capacitance of up to 1 farad (F), pouch-type EDLCs are suitable for three main applications: power assist, power backup and micro energy storage.
In a power assist scenario, the pouch type EDLC can provide power under heavy or peak loads. The pouch type EDLC can also provide emergency power to, for example, ensure a controlled shut-down when a battery is being removed or is temporarily dislodged. Similarly, a pouch-type EDLC can let a solid-state drive store critical data before its power fails.
In smart endpoints that use harvested power, EDLCs can be a handy way of compensating for the inconsistent and intermittent nature of harvested energy. Its construction gives EDLCs a greater energy density than any other type of capacitor, in the range of 3~5 Wh/kg (though this is two orders of magnitude lower than that of the commercial lithium-ion batteries).
The technology also performs well in applications where physical space is limited. Basically, EDLCs don’t heat up much in normal use. There’s no need for cooling technologies such as forced air or a heatsink. An EDLC can continue to operate when operating temperatures fall below 0°C. However, continuous charging and discharging can cause a slight temperature rise.

EDLCs need no special charging circuitry; charging takes place by applying a voltage equal to the EDLC rated voltage. Unlike a conventional battery, EDLCs do not exhibit any degradation because of deep discharging. They are also durable enough to survive a short-circuit on the output, which also helps simplify the power management circuitry. But as with any energy storage technology, they should not be over-charged.
EDLCs can be paralleled or connected serially to increase capacity or voltage. Treat each EDLC as a separate device and incorporate load balancing in the design so all EDLCs see the same charging voltage. This measure helps ensure each device delivers a typical 1,000 hours of operation at the maximum rated temperature and voltage.
At the end of the day, pouch EDLCs offer a small outline and good energy density in a flexible, light format. This option gives engineering teams greater design freedom without introducing design complexity.
Leave a Reply