Electric motors – from tiny ones which advance a sheet of paper, to huge ones which power industrial machinery — are so common that we may not give them adequate consideration. Motors have a complex history and genealogy, which can be confusing to newcomers, Figure 1. Each motor subtype has unique characteristics which make it a good fit for a certain class of applications.

Despite the apparently convoluted family tree, the vast majority of motors in use today fall into one of three categories: alternating current (AC), brushed direct current (DC) and electronically commutated (EC) motors. Note that for every general statement about a particular type of motor, there will be exceptions; that’s the nature of the complex world and family of these electromagnetic-based transducers which convert electrical power into mechanical power.
Part 1 of this FAQ will look at basic AC and DC motors; Part 2 will look at EC motors (and their sibling, stepper motors).
Q: What are the most-important motor parameters?
A: While the answer depends to some extent on the application, in general, they are:
- Operating voltage and current (nominal and peak)
- Output speed (rpm) and torque
- Maximum load
- Acceleration (start)/deceleration (stop) rate
- Stall current
- Maximum operating temperature
- Size, weight, cost
Q: What is the AC motor?
A: The AC motor has a long history dating back to the earliest days of AC power generation. It is a very simple motor design which uses the naturally occurring reversals of the current flow (and voltage) to reverse the magnetization of the coils, thus inducing rotation in the rotor, Figure 2. The rpm of the AC motor is a function of the number of windings around the circumference as well as the AC line frequency. In the AC induction motor, a rotating stator field is created by the AC input voltage, while the rotor field is induced by the stator field; in the synchronous AC motor, the needed magnetic field is generated by a current delivered through slip rings or permanent magnets.
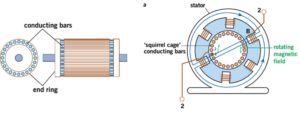
Q: What are the key attributes of the AC motor?
A: Especially for the induction-type AC motor, there is a high degree of long-term reliability since there are no moving contacts except for the rotor bearings. The AC motor has a limited rpm range, as the line frequency is fixed, and only the voltage can be changed, but reducing the voltage also reduces torque and efficiency.
Basic AC motors are best suited to situations where the load is known and constant since a well-matched AC motor can provide acceptable efficiency in many cases (though not as high as other motor types). Outside the range for which the motor is designed, efficiency drops rapidly.
Q: Where are AC motors used?
A: Until a few decades ago, they were used in a wide range of situations, from sub-horsepower size on appliance up to large industrial motors at tens or hundreds horsepower. In recent, years, the availability if low-cost, high-performance electronic components (to be discussed later) has pushed them out of the lower and mid-range, and now they are usually found in higher-power applications or lower-power ones which need only limited control, capability, or efficiency.
Q: What technology advances have improved AC motor performance?
A: Variable-frequency drive (VFD) for AC motors has changed the situation and greatly improved it. In this approach, the AC line at 50/60 Hz (or another frequency) is converted to DC, then goes to a power converter which transforms this DC in an AC signal at a different, controllable frequency, Figure 3. In this way, the motor rpm and torque can be adjusted within a fairly wide range. Note that this converted AC waveform is not a pure sine wave; instead, it is a created as a pulse-width-modulated (PWM train of signals, but the motor still operates effectively. The variable-frequency drive has greatly extended the viable application span of the AC motor; for example, the Tesla electric vehicle uses an AC motor at each wheel.
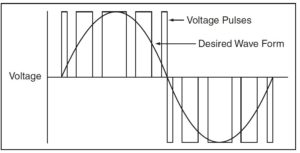
Q: What is the brushed DC motor, and how does it compare to the AC motor?
A: Like the AC motor, the DC motor has a very long history. In the DC motor, the current through the coils is reversed (or commutated) by a pair of brushes usually graphite) which make contact with conducting commutator points of the rotor, Figure 4; as the rotor turns, the brushes reverse the flow of current and thus reverse the magnetic field repulsion/attraction which induces rotation.

Q: What are the main attributes of the DC motor?
A: It has simple construction and requires just two wires for power; no controller is needed for basic operation. As there are no electronics, the motor can operate at higher temperatures. Speed can be adjusted over a modest range by adjusting the voltage, although torque decreases as the speed increases. Maximum speed is around 10,000 rpm, but some special designs can reach 5-10× that speed. Like the AC motor, performance can be acceptable (efficiency, torque, rpm) at a designed-for load and situation, but falls off rapidly outside that “sweet spot.”
Q: What about the brushes?
A: Although the brushes do wear (which is a long-term reliability issue), they can be replaced; also, as the brushes wear, they create conductive dust which can cause problems for the rest of the circuitry. Brush/motor contacts also will spark at higher voltages, which is unacceptable in many applications to due resultant EMIU/RFI generation as well as potential for explosion in hazardous atmospheres.
Q: Where are these basic DC motors used?
A: They were widely used where only a DC source was available, despite their issues with brushes and controllability. As with the AC motors, the availability of power-related electronics (controllers and switches) along with improved magnets has changed that situation. Now they are mostly used in low-end applications, such as toys, where long-life and controllability are not priorities, while their low cost and simple drive (just connect two wires to the battery) are advantages.
Part 2 of this FAQ will look at how electronic-power components have radically transformed motor design and use.
[…] Part 1 looked at basic AC and DC motors which do not require “electronics” to operate (although the variable-frequency AC motor is an important exception). However, the development of fast, low-resistance all-electronic switches – primarily MOSFETs as well as IGBTs – and microcontrollers, plus powerful permanent magnets has dramatically changed the situation. […]