Traction motors are optimized for locomotives, EVs, elevators, and other situations where high torque at start-up and low speed is needed.
Motors are an essential part of many system designs, yet their diverse variations are a mystery to many electrical engineers and a surprising number of mechanical engineers.
There are several reasons for general confusion about motors:
They often have a deceptively simple electrical schematic that does not really show the all-important specifics of their construction or capabilities.
Advances in motor-related control algorithms and power-switching devices mean that older limitations and “conventional wisdom” may no longer be valid, especially as advancements make specific motor types viable in situations where they previously were not a good option.
Further, it’s very hard to associate a given motor type with an application or class of application; the reason being that the same general type of motor may be a good or bad fit in an application depending on the many specifics and objectives of the situation such as power, torque, speed, weight, cost, and size.
You can’t do neat, clean, one-to-one, or one-to-many mappings of motor type to application class. Motor family trees do not help, as they focus on motor design rather than their applications (Figures 1 and 2).


For example, many engineers consider the classic brushed motor to now be useful only for low-end toys or products which do not need tight control of motion characteristics and would likely dismiss it for an advanced application. However, a recent design example of a medical infusion pump shows that with modern motion control, the brushed motor may be the best choice to meet the multiple performance objectives of the sophisticated design (see EE World, The brushed DC motor: Still a very viable option, Part 2: Applications).
This FAQ will focus on motors for one application: traction. It looks at electrical and mechanical issues of the motor itself, as well as installation and drive electronics.

Q: What is a “traction” motor? How do its primary performance characteristics differ from other motor applications or types?
A: The general requirements of traction motors are significantly different from motors for industrial motors, even of similar power ratings. Traction-motor applications usually require high torque for low speed for start-up acceleration, low torque for high-speed cruising, frequent starts/stops, and a very wide speed range of operation (Figure 3).
In contrast, industrial motors are generally optimized for a more limited range of operating conditions, generally operate in enclosed spaces even if they are in a harsh environment, and often are not mobile.
Q: What makes a motor a good traction motor?
A: It is not the motor type, although some types are better suited for traction than others; for example, a series-wound AC motor is better for low-speed torque than a shunt-wound one. The key factor for a suitable motor, however, is the physical construction, the amount of copper wiring, the way the copper windings are arranged, the amount of iron, and the lamination layout in the motor. The electrical schematic of a traction-optimized and a non-traction motor may be the same “on paper,” but the physical details are very different.
Q: What vehicles or applications use traction motors?
A: They are used in railway locomotives (both diesel-electric and overhead catenary-powered all-electric), urban light rail vehicles (LRVs–also called trams), and suburban LRVs. They are also used in automotive electric vehicles (EVs), of course, an application that has spurred R&D in mid-range traction motors as well as their driver circuits and components).
They are also being adopted for electric drives in heavy construction equipment (e-machines), where they are powered like a diesel-electric locomotive with an onboard fuel tank and a fixed-speed diesel engine driving a generator to power the various motors (Figure 4).
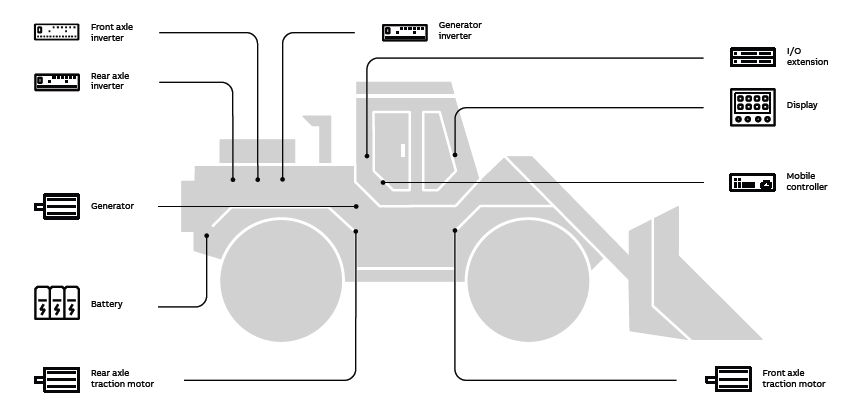
Figure 4. Electric-based drivelines using traction motors are now being used in some heavy equipment, with a diesel-driven generator as the primary electrical power source (image: ABB).
Elevators and escalators, material handling equipment, and conveyor belts are also traction-motor applications, although the motor is not mobile in these situations.
Q: What are the power levels of traction motors?
A: They span tens of horsepower to several thousand horsepower (roughly ten to several thousand kilowatts). The lowest value might be for an electric forklift truck which only operates at low speeds and where acceleration is not an issue, while the latter would be for a full-power railway locomotive. A typical electric-vehicle traction motor is rated at around 200 kW.
Q: So, all train motors have the same design, except for power (size)?
A: No, there are DC series-wound motors, single-phase AC series-wound motors, and the multiphase AC drive (not the same as single-phase AC). The right choice is a function of many factors, but technical advances in, and advantages of, modern motor-control electronics have pushed most new designs to multiphase AC drive.
Q: Where is the traction motor mounted in the application?
A: With few exceptions, the traction motor is mounted on or in part of the axle of the wheel it is driving. It is a direct-drive system with minimal or no intervening gearing. This is to minimize size and weight while reducing the parts count and thus enhancing reliability.
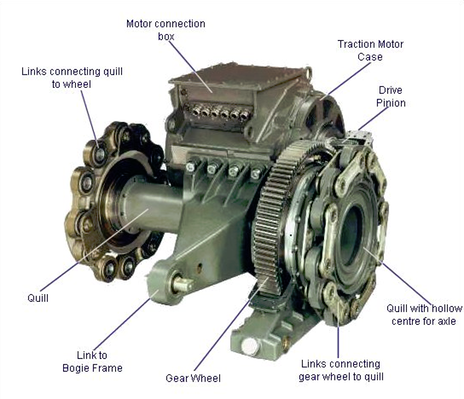
In most locomotives, there is one motor per axle on the train “bogie” (Figure 5). (The bogie is the chassis or framework that carries a wheelset and is sometimes called a “truck.”) One of the design challenges in railroad designs is to get as much of the motor weight as possible off the un-sprung wheel axles and onto the sprung part of the bogie for better stability and handling.
For lighter-service engines, only one axle is powered, and the other axle is unpowered. In other cases, there is one motor powering both axles of the bogie, called a mono-motor bogie. The arrangement used depends on the vehicle size, required speed, weight, and other factors.
Q: In general, what is the operating environment for traction motors?
A: In most installations, traction motors lead a “hard life” with respect to shock and vibration, temperature extremes, exposure to dirt and debris, and start/stop operation. Further, their relatively high-power levels necessitate heavy electrical conductors, cable portions, and connectors.
The next part of this article looks at the different types of traction motors in more detail.
Related content
The brushed DC motor: Still a very viable option, Part 1: Operation
The brushed DC motor: Still a very viable option, Part 2: Applications
Electric locomotives and catenary power systems – Part 1: basic functions
Electric locomotives and catenary power systems – Part 2: power needs
Electric locomotives and catenary power systems – Part 3: power delivery
Electric locomotives and catenary power systems – Part 4: maintenance and corona
Basics of motion-control profiles, Part 1: Context
Basics of motion-control profiles, Part 2: Ramp profiles
Basics of motion-control profiles, Part 3: Implementations
Motor fundamentals and DC motors
SiC gate driver benefits traction inverters for EVs
Discrete 750-V IGBTs optimized for automotive traction inverters
Full SiC power module optimized for electric/hybrid traction motorsports apps
IGBT power modules optimized for EV traction inverters
Magnetic gear tooth sensor IC optimized for traction motor apps
Wide-input-range, high power density dc-dc converters optimized for railway traction, rolling stock apps
External References
Medical Design Briefs, “Every Drop Counts: Designing Motors to Optimize Home and Ambulatory Infusion Pumps”
Electrical Desk, “Different Types Of Traction Motors”
Everything PE, “What is an Electric Vehicle Traction Motor?”
Wikipedia, “Traction Motor”
Springer, “Vehicle Traction Motors”
The Railway Technical Website, “Electric Traction Control”
ABB, “ABB traction motors — Light rail vehicle (LRV)”
ABB, “Let’s go electric now! Advanced e-mobility drivelines”
Monolithic Power Systems, AN047, “Brushless DC Motor Fundamentals”
Curtis-Wright, “CWTI-D420 New Generation Dual Traction Inverter Sales Brochure”
Curtiss-Wright, “Traction Inverters Data Sheet”
Texas Instruments, “Technical White Paper Design Priorities in EV Traction Inverter With Optimum Performance”
Texas Instruments, “Design Priorities in EV Traction Inverter with Optimum Performance”
Texas Instruments, “Enhance the Design of HEV/EV Traction Inverter Systems Using Isolated IGBT and SiC Gate Drivers”
With proven 8x peak torque in the same package of any other electric motor system, SYNCHRO-SYM is the best traction motor available, and without rare earth permanent magnets